On 16th September 1966, speaking at a reception, the Chairman of Associated Shipbuilders, Sir John Hunter announced, “that without any further capital expenditure, they could build a tanker of no less than one million tons deadweight ……..” .
This suggestion would take shipbuilding on the River Tyne, the birth place of deep sea oil tankers, into a different league altogether.
This was the era when tanker operators were in a headlong stampede for building berths, as tanker capacities escalated worldwide.
The growth of the oil tanker really took off from the end of World War II, the T2s with a deadweight of 16,800 tons were the norm. As the world’s industries started to re-build after the devastation there was a consequential increase in the demand for oil to fuel the burgeoning tiger economies. This meant an expansion and increase in the output from the refineries.
The tanker operators reasoned that if they could build larger ships then the transportation price for a barrel of oil would reduce, and by doubling the dimensions of a T2 tanker, such a ship would carry eleven times the quantity of oil.
The United Nations instituted the Intergovernmental Maritime Consultative Organisation (IMCO) in 1948, which would issue various protocols to oversee the safe operation of oil tankers.
The industrialised nations struggled to meet the demand for steel, as Governments strove to re-build nations’ economies after the war, this lead to policies to ration supplies of steel etc. This created a situation where ship owners were reserving building berths in the shipyards, years in advance of their needs. The Anglo Saxon Petroleum Co. Ltd. led the way after World War II, when it ordered four 28,000 dwt tankers. The first to be launched was the Velutina from Swans, Wallsend yard by H.R.H. Princess Margaret on 4th April 1950.
As oil demand and refineries expanded in the 1950s so did the size of the ships with new regulations, scantling and freeboard upgrades from the classification societies, and during the decade leading to a steady rise in the size of ships.
British shipyards were hampered for space as the urban sprawl of previous decades had hemmed them into what in earlier decades were considered ample room for the industry. The UK yards also went through vast modernisation programmes in the 1950s and 1960s to improve productivity as they moved away from outdated and time consuming building methods.
The shipyards on the River Tyne had been merged under the Geddes Report in 1966, taking the name Associated Shipbuilders, a name which was pretty quickly dropped in favour of Swan Hunter & Tyne Shipbuilders, under the Chairmanship of Sir John Hunter.
The design team was led by the technical director Dr. Fred Taylor, and in 1966 stunned the general public on Tyneside with plans to build a mammoth tanker. The ship would be 1,722 feet long (o.a.), with a beam of 250 feet, depth of 140 feet. The ship would have a deadweight of 915,958 tons, with a cargo capacity of 43,574,560 cubic feet, giving a loaded displacement of 1,107,473 tons on a draught of 105 feet, with a block coefficient of 9124. Twin Sulzer 12 RND 105 engines of 80,000BHP giving a speed of 14.3knots, while using 392 tons of fuel a day at sea, the propellers would weigh 65 tons each.
As an alternative, a paper was submitted a little later to the Institute of Marine Engineers by three of its members, who suggested an alternative machinery configuration, they argued that a twin screw ship with two rudders and possibly twin skegs’ which would add to the ships underwater resistance was not perhaps the best arrangement and that a triple screw ship might be better, having a central propeller and widely space wing propellers, preferably controllable pitch, which could be used effectively at slow speeds when manoeuvring.
It was estimated that the ship would cost L40 million to build, with daily running costs of L5,120!!
The ship would have a seven deck high accommodation block for the 44 crew. The ship was too big to build in one piece so would be built in halves. The estimated launch weight for the aft part would have been 71,700 tons and the fore part 73,400 tons. It is not known what the Tyne Improvement Commissions attitudes were with regard to any damage that might be caused during launches, and the effects on the environment with the amount of water displaced during the launching process. Along with all the dredging that would be needed, and disruption to the normal flow of river traffic, passing up to the deep sea berths Newcastle Quayside and beyond.
The tank arrangement consisted of ten centre tanks no longer than 150 feet and twenty six wing tanks for cargo oil, and eight wing tanks for clean water ballast totalling 28,310 tons. IMCO also insisted on Nos 1–4 tanks had double bottoms for sea water ballast as a precaution against grounding. As there were no drydocks big enough to take such a structure, at the time, these would be joined by the means of a cofferdam placed around the exterior of the ship large enough for the construction team to weld the two halves together – quite a task !
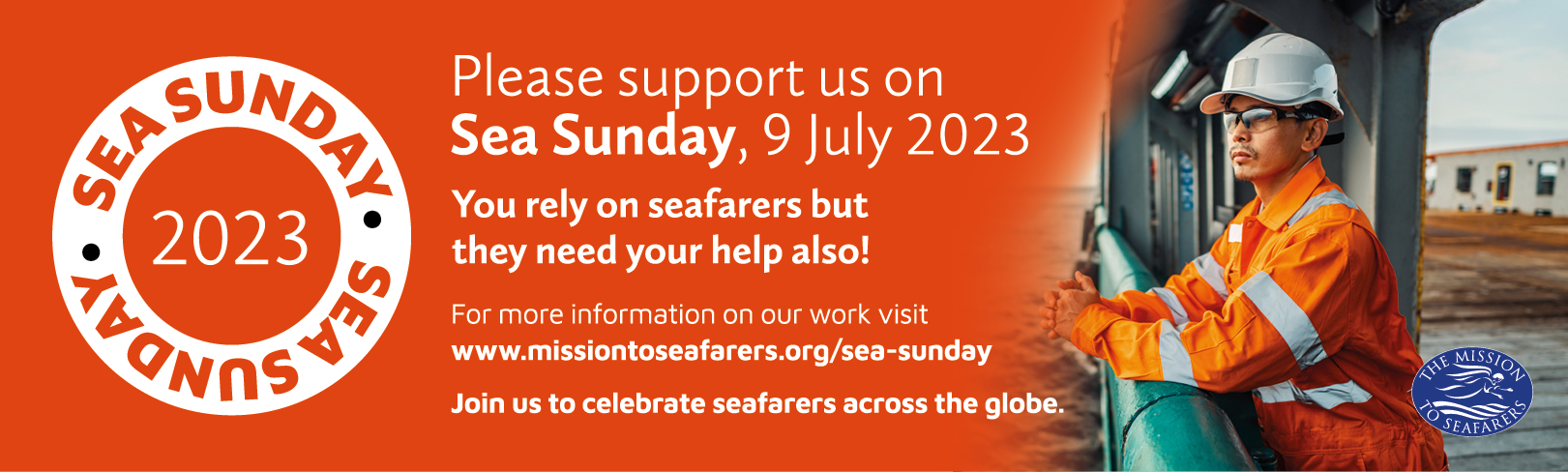
Other options included creating a new yard on the river with a large building dock. While Swans looked at the larger ship, and considered designing a 650,000 dwt ship, Harland and Wolff carried out similar studies on a 500,000 dwt ship. Finite element calculations were carried via BRSA’s computers, the National Physical Laboratory, Naval Constructors Research Establishment, and of course Lloyds were all involved in the project overseen by the Ministry of Technology with a fraction of the development costs. At the same time Det Norske Veritas were developing their regulations for 500,000 dwt vessels. Their view was that a one million deadweight ship was technically feasible, but it would depend on shipowners, brokers, insurance experts, and yard owners as to the economical and practical considerations of such a vessel. Although I have seen no evidence it would be safe to assume that the Japanese would also have been looking at the same options too.
Operationally the report suggested the following scenario that a fleet of three, one million tonners making 4.53 voyages per year could do the work of ten, 260,000 tonners. Transporting 12.8 million tons of crude a year from the Persian Gulf to Europe. Such a small number of vessels would introduce further risks into the transportation systems, a risk of loss or damage, time for repairs, and problems with scheduling .
The additional costs of upgrading and expansion of existing refineries to cope with were not factored into the costs of the proposed ships, but it was thought that the cost of these upgrades, would wipe out about half of the freight saving costs that a million deadweight ship might accrue, and savings would be more realistic if ship owners built ships of between 400,000-600,000 dwt ships.
Because of the ships large loaded draft, the discharge of the cargo was an issue. The cheapest option was to discharge at single buoy moorings, which could be disrupted by weather or the fact that different refineries might require part of the cargo. This led onto the possibility of the use of a transhipment terminal, 500 miles short of the refinery such as Bantry Bay. Lightening at sea, in the western approaches, as severe restrictions would be imposed if the normal route had her using the English Channel, another costly option, was also considered and it was thought likely that 400,000 tons would have to be off loaded to reduce the ships’ draught sufficiently to about 20 metres so she could enter existing ports. This would require either six 70,000 dwt, or two 200,000 dwt shuttle tankers, however this operation was thought to take two or three days, with risks of delay and the integration of schedules of up to seven different ships.
The study of the proposed ship suggested that around half the freighting cost advantage could disappear in the additional costs incurred, such as transhipment or additional shore investment. A 400,000 to 600,000 dwt size of tanker could probably achieve more easily a 10% saving per ton in shipment costs compared with a 250,000 dwt ship, rather than the 20% saving assumed for the million tonner. In the end only a handful of half million deadweight ships were built, with several of them ending up as FPSOs or storage vessels, which proved in time, the limit of risk the oil companies and their insurers were prepared to go to.
Meanwhile in the far east and elsewhere in Europe vast modern shipyards were being created from global sponsored reconstruction funds. These yards used production line techniques, the only one in the UK to compare was the building dock in Harland & Wolff’s yard which came on stream in 1968. In the previous year Verlome announced plans to build two docks and one slipway at Rosenberg capable of building ships of 900,000 dwt, while Japanese builders joined the stampede to provide new yards on green field sites, at the same time as offering heavily discounted prices for the ships, charging less for the steel required for overseas contracts, while Japanese domestic ship owners paid the going rate.
A 250,000 dwt tanker would require 30,000 tons of steel to build. Meanwhile the economics in the UK for building large tankers were such that in 1969 a 200,000 dwt tanker would cost L25/deadweight ton, while a 100,000 dwt ship would cost L33/deadweight ton, and that building one 200,000 dwt ship would cost L300,000 less than building two 100,000 dwt ships. Not all tanker operational requirements were discussed for the million deadweight ship in the paper, some of the issues which would have needed resolving were:
– Tank coating integrity, inspection and maintenance when dealing with a highly corrosive cargo. – Drydocks, although some were in the planning stages.
Welding higher tensile grade of steel, if used, to reduce the lightship, and consequently increase the deadweight on the same draft, would have to be reviewed because of the hogging and sagging and stresses incurred, that could lead to weld fractures on such a vessel in cold waters. Due in part to the lack of experience of welding plate of up to 50mm thick
IMCO might impose anti-pollution and revised safety requirements which could impact the cost of the project. Following the Torrey Canyon disaster in March 1967, not only were operators but the general public becoming acutely aware of the consequences of the transport of large volumes of oil. This led to IMCO imposing MARPOL (Marine Pollution) Protocols on the industry. While there had always been cases where some Captains had dumped their cleaned tank residue into the open sea, the problem has not registered with the general public until the accident. The thought of a ship carrying ten times the amount concentrated the mind. Once again while there had always been instances of tanker explosions while tank cleaning, the reasons why were not fully understood until the mid 1970s after a series of VLCC accidents in a matter of weeks. Created by a fine water spray system that in some cases, could become electrically charged, thus causing an explosion. This induced further study leading to crude oil washing followed by the inert gas system. The month before the design of the 1million dwt tanker was announced by Swan Hunter, British Crown had blown up when loading 25,500 tons of crude oil at Umm Said with the loss of 19 lives, due to a spark from an electrical motor. The problems surrounding all these issues were yet to be addressed.
The stopping distances of a 200,000 dwt ship take 2.5 miles to make a crash stop, while to alter course 20 degrees would take one minute twelve seconds during which time the ship will travel one and a half ships lengths. Food for thought when manoeuvring a one million deadweight ship!
Pipe couplings for cargo pipes of more than a metre in diameter would need to be developed using know-how from the offshore industries.
Areas in the engineering spaces such as shaft seals, stern glands would have to be up graded, and easy access created for maintenance etc.
It was thought unlikely at the time that any oil terminal had the capacity to absorb one million tons in one cargo, or its storage and whether they had the depth of water to take such a vessel. One option put forward by the Onassis Technical Group a few years later suggested the ambitious ‘Delta’ system, which involved a mother ship carrying four 250,000 dwt ‘caissons’, in a piggy back fashion. On arrival at a pre-determined point offshore, the mother ship would be ballasted down, and the caissons would then be detached and towed away to exiting shore terminals. The mother ship would have all the propulsion, accommodation and navigation systems. Each caisson would have its own cargo pumping system and would be towed to a reception port while the mother ship remained off shore. As these caissons would have a draught of 33 metres another option proposed by the design team, would be to ballast the caisson so that it rolled over onto its side, thereby reducing its draught, so it could enter a port which was shallower. No details were revealed as to how the caissons would be attached to the mother ship which would had to have been substantial to say the least.
Another concern was the volatility and fickle nature of the geopolitics of OPEC and the oil supplying states and guarantees of safe passage.
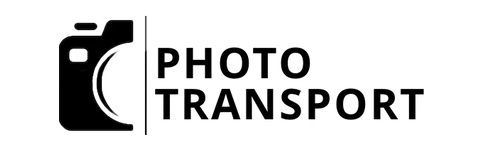
In October 1974 Swan Hunter’s Technical Director Dr. Fred Taylor said, “in certain sectors of the market for new ships there was an increasing tendency for severe random disturbances to occur for which there was no control or forecast capability, such as the wars in the Middle East, foreign government stimulation and OPEC production restrictions”. The price spike by OPEC in 1973 when they increased the price of a barrel of crude four fold led to large lay ups throwing the markets into turmoil. As an example British Respect a brand new 277,000 dwt ship completed in September 1974, went into a long lay up on delivery from the Japanese shipyard. These factors made operators wary of committing large sums of money to projects, which could be highjacked by events. The crisis for shipbuilding worldwide was reached in 1975 by over ambitious expansionist polices by shipyards in the far east, leading to a total collapse of the tanker market. A few months later, the much vaunted Swan Maritime deal, which would have given work to the yards on the Tyne for a decade, building tankers, lay dead in the water, along with plans to create the world’s largest ship.
Comments
Sorry, comments are closed for this item