The Rakaia
By David Carpenter
Owners of Rolls-Royce motor cars used to say their cars never broke down, but on rare occasions only, ‘failed to proceed’. This was how our old Chief Engineer, Jock Cowper described a potentially dangerous situation that occurred when New Zealand Shipping Company’s Cadet ship the 8,213 gross tons M.V. Rakaia was just passing the Galapagos Islands, homeward bound from New Zealand to the U.K. in 1964, with a full cargo of frozen lamb and apples from her adopted port of Nelson.
It occurred a few hours after transferring fuel that we had taken on in New Zealand from the double bottom tanks up to the settling tank then down to the purifiers, then back up to the daily service tank. The Rakaia was unusual in that it ran on gas oil rather than heavy oil.
The trouble first manifested itself during my watch the 12 to 4 (known as the graveyard watch). The Second Mate phoned down to the engine room and said we were making quite a bit of black smoke, at the same time I noticed the main engine had lost a couple of revs. A quick check on the all the pressures and temperatures showed no abnormalities, however I phoned the Chief Engineer to keep him informed.
The Chief replied, “Och eye Three O, I noticed the wee droop in revs. We are probably hitting the Humbolt Current, keep a close eye on things especially the sea water temperature”.
The Chief rarely visited the engine room, but he somehow knew how his main engine was behaving without going below. A few weeks earlier after coming off watch, I went along to his cabin to hand him a set of indicator cards that I had just taken.
As I handed them to him, he said, “We’ve a wee bit of trouble brewing on six and eight top pistons”.
When I previously worked out the readings I noticed that the compression was slightly down on those two units. I was about to mention it, but he beat me to it. I must have given him a look of surprise because he said, “Lay down on the day bed, put your elbow on the backrest and the palm of your hand over your ear”.
I followed his instructions.
“Well what do you hear”.
“Just the usual rumblings from down below Chief”, I replied.
“Can ye nay hear it Three O, the old girls nay running reet”.
I don’t know if he was having me on, but on several occasions I had seen him reclining on his day bed, reading one of his Western novels with his arm in this position. This was one of the reasons that he didn’t have to visit the engine room. One of the others was that he trusted his engineers implicitly and would have nothing said against them, especially in the dining saloon.
After phoning the Chief about the slight drop in revs, I instructed the Sixth Engineer to keep a close watch on the exhaust temperatures while I monitored the sea water temperature. When encountering the Humbolt Current from the West the sea temperature suddenly drops, unless precautions are taken, it can result in cracked cylinder liners.
When I came off watch at 4am I updated the Second Engineer who was relieving me with the situation. He suspected it was the fuel that we had taken on in New Zealand and had just started using, so it was decided to transfer it back to the double bottom tank and use it for the boiler when in port.
After getting cleaned up I was having a couple of beers with the Sixer just before turning in, when the alarm started ringing in the allyway.
All the off-duty Engineers including the Electricians and the Freezers all rushed out of their cabins just wearing their Y fronts, that is except the Chief who was wearing his pyjamas and carpet slippers.
The main engine had stopped, when we got below the Second said the engine had what we called ‘Gassed Up’, so we were not too concerned, however the Chief was not happy about things.
This was an occasional thing that tended to happen with Burmeister & Wain Double acting two stroke engines. During the voyage we had already experienced thison two occasions.
After we bled the fuel system, the Chief asked the Second to stand by the bottom indicator cocks and myself to stand by the top ones and everyone else to leave the engine room and wait by the Engineers Mess Room just inside the deck entrance to the engine room.
This precaution was because a couple of years earlier a Union-Castle Line ship, the Capetown Castle, was manoeuvring prior to docking at Las Palmas. She was powered by a pair of ten cylinder B&W double acting two strokes, whereas the Rakaia had one eight cylinder main engine of the same design. When Capetown Castle’s Second Engineer put the Port engine astern, a fire ball engulfed the engine room, killing six engineers and a greaser.
The cause was traced to a small quantity of oil in the air start system that ignited and blew back then exploded and sent a sheet of flame through the engine room. This disaster was well known to us engineers on the Rakaia, so we were well aware of the possible unintended consequences.
The Chief took the controls and phoned the bridge to say we were ready to start. I heard the telegraph ring followed by starting air whooshing through the cylinders. I had shut number one cock and was heading for number two. There were long streaks of flame shooting from the indicator cocks ahead of me, the ship was then shaken by a huge explosion. This was followed by a secondary explosion. Everything happened so fast I just kept running towards the rear of the main engine and carried on to the short ally way to the engine room deck entrance.
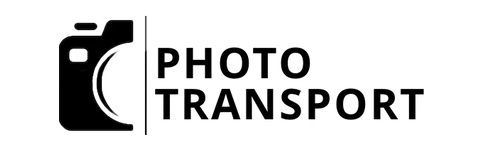
Assisted by a huge blast of hot air from behind me I dived amongst the rest of the lads who were waiting there, I heard one of them say, “Christ Three O, we thought you were a gonna there for a moment”.
When I looked back the engine room was full of smoke, with snow like pieces of asbestos drifting down. Our immediate concern was for the Chief and Second who were still somewhere below. There wasn’t time to discuss what to do, I rushed into the adjacent Mess Room and grabbed an arm full of rags. There wasn’t any water available but there were several cans of Guinness on the table, so I quickly opened them and poured the contents over the rags. I gave half to the Fourth and told the Fiver to break out the horrendous asbestos fire suit and follow us down below, I told the rest of the lads to stand by in case we needed fire fighting equipment. We wrapped the rags around our heads and shoulders then felt our way to the first flight of steps. It was much clearer by the time we reached the lower set of indicator cocks, but there was no sign of the Second. I looked down over the hand rail and was relieved to see the Chief on the phone and the Second heading for the ladder, as we met at the top, he pulled a face and said.,
“Bloody hell you smell like a brewery, have you been on the piss again.”
“No but I’ve just wasted some good Guinness coming down here to look for you”, I replied.
We all smiled and headed back up the ladder only to be confronted by the Fiver encased in the asbestos suit on his way down. We threw our wet rags at him as we squeezed by and left him to get in some fire drill practice.
“I think we may have a wee spot of bother”, remarked the Chief as he looked up at the boiler when he joined us at the engine tops, which were now coated with a layer of asbestos flakes and carbon dust.
He added, “The bridge phoned doon, I dunni think they were expecting an answer, apparently a wee flame shot out of the funnel some fifty feet high lighting up the sea for miles and a shock wave went out from around the ship. They were under the impression that the engine room had blown up”.
He told the fourth to go up and check out the boiler while the rest of us got on with removing all the fuel valves from the main engine. By now we had been joined by the Freezers, together with the Leckys plus the engine room labourers, so there were plenty of hands to sort out the mess.
The smoke had now cleared sufficiently to see that there was a gaping hole in the front of the boiler where the furnace front should be. It was now lodged on top of the piston yoke of number six unit. As it had blown out, it had taken a large area of lagging with it. Luckily the fuel pipe had sheared off after the stop valve, which had saved us from the possibility of an engine room fire. The boiler was situated on a landing at the base of the funnel about twelve feet above the top of the main engine.
The piston yoke was a huge casting, so it suffered no damage. While the labourers, under the supervision of Ray, the Chief Lecky, got on with the job of lifting the furnace front off it, the rest of us got on with removing the thirty two fuel valves from the main engine.
One of my responsibilities was to make sure we always had at least that number ready to fit, in such an occasion as we now found ourselves.
The cause of the problem was soon revealed when we found that one of the valves had most of its nozzle missing. This had allowed the combustion pressure to get into the fuel system causing an airlock which stopped the engine. When we bled the fuel system it allowed the fuel to pour into the combustion space, culminating in the big bang that required the watch up on the bridge to seek out a clean set of underpants.
The Chief was concerned as to the whereabouts of the missing piece of fuel nozzle. It may have been blown out of the exhaust port or it may still be sitting on top of the piston, waiting to do severe damage when the engine was started.
We fished about through the fuel valve apertures with a magnet screwed to the end of a rod, but had no luck! As the faulty valve was in a lower combustion chamber, we would have to strip out both the top and centre piston to make sure it wasn’t there. With the ship rolling about this would have been a time consuming and dangerous job.It was thought that we still had a chance if someone would crawl through the bottom exhaust manifold and check out the combustion space through the exhaust ports.
‘Kiwi’, our Sixth Engineer drew the short straw. While he wrapped rags round his elbows and knees we removed the end cover from the manifold and engaged the turning gear and hung the ‘Turning Gear In’ notice on the controls.
This was an early sort of Health & Safety procedure that was always done when working on or in the main engine. In our present situation, with the ship laying beam on to the seas, it was quite possible that a wave could give the propeller a bit of a turn. If ‘Kiwi’ had his arm through one of the ports at the time, it would be neatly sliced off.
After we tied a length of rope to both his ankles he crawled into the manifold trunking clutching a torch in one hand and the magnet in the other. After about five minutes, to everyone’s relief, he shouted that he had found it, and backed out of the trunking brandishing the piece of nozzle on the magnet but looking like he had been liquidized.
While ‘Kiwi’ had been doing his bit we fitted a temporary cover plate over the gaping hole where the burner had once been. We fitted the set of valves that I had previously reconditioned, and bled the fuel system in readiness to get under way.
We also checked out the boiler heating exhaust flap valve, this had been shut when the engine had gassed up. However it was found that it had not completely closed, allowing some of the explosion to divert through the boiler and cause the damage.
There wasn’t a lot we could do in our present predicament except to work the operating ratchet back and forth in the hope of shutting it. We had to take turns doing it as the temperature up behind the boiler was in the region of a hundred and forty degrees. The only ones exempt from this were ‘Kiwi’, who was still trying to hydrate himself, giving us concern as to the possibility of a spell of water rationing. The other was the Chief on the grounds that the soles of his carpet slippers might melt down.
To the amazement of the bridge we were under way in just over two hours. We were lucky to have got away with it so lightly. That morning at breakfast the ships doctor who was on his first trip and rather naive, put his foot in it again by saying to the Chief,
“I hear we broke down again last night Chief.”
“We did nay brrek doon Doctor, we just failed to proceed for a wee while.”
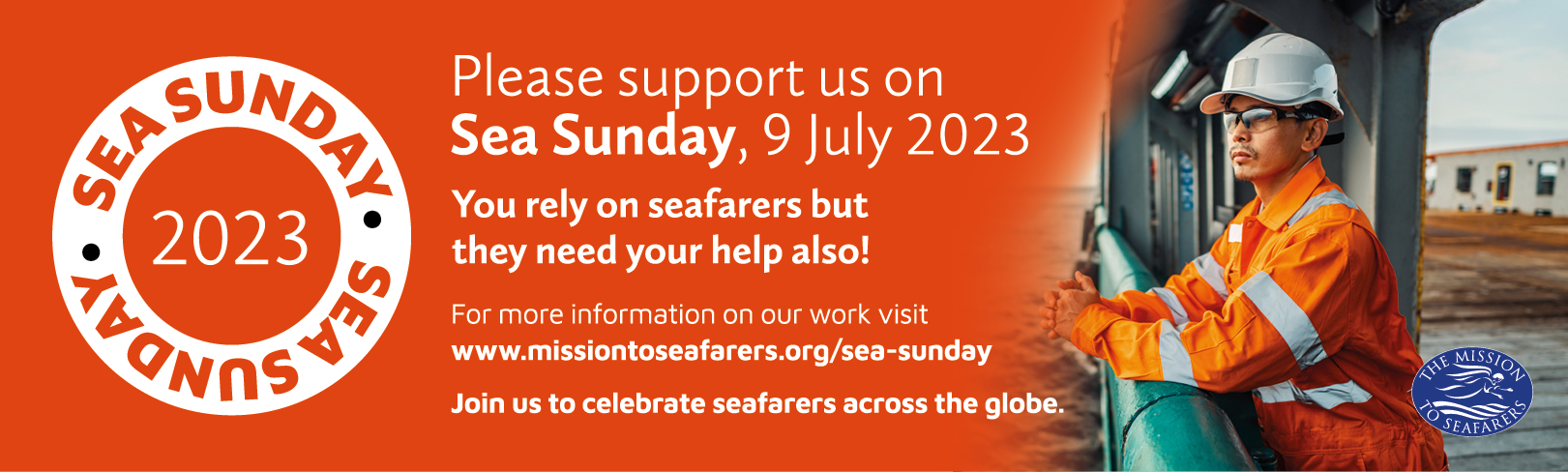
Comments
Sorry, comments are closed for this item