On 4th March 2020, Ōita Prefecture in Japan announced that it would reintroduce the hovercraft as a means of public transportation connecting Ōita Airport in Kunisaki with the central area of Ōita City in 2023. There had previously been a hovercraft service here, operating on the same route 1971-2009. When this ceased, Hovertravel’s Ryde-Southsea service across the Solent became the only year-round passenger hovercraft service in the world. The Ōita Prefecture allocated a budget of ¥7.5 billion to restart the operation due to an increase in throughput at Ōita Airport. Travel time by hovercraft was estimated at 25 minutes between the two points. Ōita Prefecture has 472 miles/759km of coastline and is situated in the north-east of the island of Kyūshū. It measures 74 miles/119 km from east to west, and 66 miles/106km from north to south. The island is surrounded by the Suo Channel, with Honshū Island to the north, the Iyo Channel and Shikoku Island to the east. The adjoining Prefectures are Miyazaki to the south, and Fukuoka/ Kumamoto to the west. Ōita is the capital with other major cities including Beppu, Nakatsu, and Saiki. The Prefecture is on the Bungo Channel, connecting the Pacific Ocean and Seto Inland Sea and is famous for its hot springs and a popular tourist destination.
Hovering History
The home of the hovercraft is the United Kingdom with the history dating back to the development of the SRN1 by Sir Christopher Cockerell. This experimental craft was built by Saunders Roe and first hovered on 11th June 1959. East Cowes on the Isle of Wight was a thriving centre of hovercraft production for Saunders Roe/Westland with the SRN2, SRN5, SRN6 and cross-channel SRN4 (1968) variants all being born here plus the BH-7. The first passenger-carrying hovercraft to enter regular service was the Vickers VA-3 in the summer of 1962, carrying passengers along the north Wales coast from Moreton, Merseyside, to Rhyl. Hovertravel Ltd. opened its passenger hovercraft service between Ryde, Isle of Wight, and Southsea (Portsmouth) on 24th July 1965 using 38-seat SRN6 craft and the operation went from strength to strength, predominantly using SRN6 craft. The 1980s brought a new era in hovercraft when the first AP1-88 was built, namely the Tenacity, which joined the Hovertravel fleet officially in 1983. This craft was fitted out at Hoverwork’s base in St. Helen’s, Bembridge Harbour, I.o.W with other such craft following for the Ryde operation and elsewhere around the world. Hoverwork had begun operations in December 1965 to support Hovertravel and to maintain/build craft, firstly at Dinnis Yard in Cowes and then at Woodnuts Yard in St. Helen’s from 1974. Hovercraft construction and maintenance at the BHC/GKN Westland East Cowes premises was phased out so that left Hoverwork Ltd. representing the industry on the Island. Across on the mainland, Griffon Hovercraft Ltd. was founded in 1976 in Southampton and launched its first diesel-powered hovercraft, the 1000TD, in 1983. During 2008, Griffon Hovercraft was acquired by the Bland Group, the same year that the group increased its shareholding in Hovertravel Ltd. from 25% to 99.92%.
In 2009 Griffon Hovercraft was merged with two other hovercraft specialists, Hoverwork Ltd. and Hovercraft Consultants Ltd. The combined entity was branded Griffon Hoverwork Ltd. The company established a new facility on the River Itchen at Woolston in Southampton, which officially opened on 11th November 2010. Unfortunately, this ended hovercraft production and heavy maintenance on the Isle of Wight but a small maintenance facility was provided at Ryde Hoverport to service and support the craft on the cross-Solent route. With such a rich history of hovercraft design, development, operation, and manufacturing, where else should the new Ōita craft be built but in the home of hovering, the Solent region. In November 2021 Griffon Hoverwork Ltd. announced a £25 million hovercraft order from the Ōita Prefecture with construction commencing in January 2022 at their relocated premises of Trafalgar Wharf in Portchester on the former Vospers/Halmatics site. The hovercraft builder had moved along the coast from Woolston. The company was looking to double its workforce to around 160 persons and the 3 craft ordered are modified versions of the revolutionary 12000TD hovercraft that were introduced as the first of their type in 2016 and are operated by sister company Hovertravel Ltd., namely the Solent Flyer and Island Flyer. The Solent Flyer was the prototype for the new breed of craft and first visited Ryde from Woolston on 21st March 2016. On 11th April 2016 Hovertravel announced that the Solent Flyer was officially part of the fleet and commenced a 3 month period for staff to be familiarised with the new technologies that the craft brought with her. The preview for guests and media followed on 27th July with sister craft Island Flyer taking to the water in early June 2016 prior to making her Ryde debut on 23rd June during trials.
Refine & Enlarge
The Hovertravel craft remained the unique examples of the 12000TD class until this order was sealed in Japan. Work on the first hovercraft started at the end of January 2022, with delivery of all three scheduled to conclude in February 2024. The latest 80-seater 12000TD MkII trio are 23.70m long compared to the 22.00m long MkI craft with an identical beam of 12.80m (hovering) and 10.00m with skirt deflated. The height of both variants is also the same at 7.00m/8.52m (hovering). The additional length of the MkII craft is equivalent to one extra frame in the passenger cabin. The cargo capacity aboard is the same at 500kg and, as the title suggests, each craft has a 12,000kg (12 tonne) payload. Thanks to the innovative drive system, the 12000TD model of hovercraft only requires two power units comprising a pair of 12-cylinder turbocharged MAN D2862 LE124 producing a combined output of 1,586 kW (2,158 hp), enabling a top speed of 45-50 knots (92.6 km/h). These engines were specifically tailored for use in a hovercraft and the drive has been configured and perfected specifically for this use. During the development process the departments of the Marine and Off-Road market segments worked together on the project in the MAN International Engine Competence Centre in Nuremberg, Germany.
The original D2862 LE124 was intended for use with agricultural engineering because the engines are lighter and are radiator cooled. This is important because a hovercraft does not come into direct contact with the water therefore it is not possible to use the typical water-cooling system used for marine engines. In addition to various minor modifications, the special feature of the power units is that they comply with the MARPOL regulations for the shipping industry. The hovercraft version of the D2862 LE124 was first used in the MkI examples of the 12000TD. The 793-kW output is generated from a 24.24 litre capacity unit and the engines are mounted as low as possible in order to generate an ideal centre of gravity. Overall, the MAN D2862 series has a power range of 588 to 816 kW, a cylinder bore of 128mm and a stroke of 157mm. The units are 1,660mm long and 1,333mm wide with a height of 1,391mm. The main engine room air intake is located on the roof of the craft with all engine air intakes having knitmesh filters fitted to reduce water ingress. The machinery space is located aft of the passenger accommodation and is behind a fire retardant and sound proofed bulkhead which has access doors built in. Using a belt drive system, the main engines each drive a five-blade variable pitch, 3.5m diameter ducted propeller which turns at 850rpm. A large slow turning propeller reduces noise, giving a quieter ride with the average noise reading taken in the public space being 74dB, equivalent to that of office noise. The propeller blades are constructed of a natural composite core (wood) with carbon fibre skin. A nickel strip protects the leading edge of each blade. The propellers are type approved by the European Aviation Safety Agency (EASA) in a similar manner to aircraft propellers. Weight saving measures were sought due to the craft being longer, with one such reduction being in the weight of the propeller ducts by modifying how they are fabricated.
When hovering, the height from ground level to the top of the ducts is 6.88m. A set of 4 hydraulic rudders is mounted on the rear racing side of each propeller duct and uses the airflow coming from the propeller to produce a sideways force to turn the hovercraft. The physics behind this is identical to how an aircraft wing works. The rudder assembly is rotated inboard by around 17 degrees to improve stability and passenger comfort during turns. Each rudder can rotate up to 40 degrees in either direction and is constructed by folding a thin piece of aluminium around an aerodynamic shaped internal structure. Each main engine also drives a pair of highly efficient, mixed flow 0.88m diameter carbon fibre lift fans (lighter than the aluminium equivalent). These are mounted in pairs outboard of the engines, are a Griffon Hoverwork patented design and are around 10% more efficient compared to traditional lift fans used for hovercraft. A nacelle on each side of the craft, located aft of the cabin, encases the lift fans to reduce damage to surrounding areas and to minimise the inhalation of debris. The air drawn into the skirt beneath the craft provides the air cushion that makes the hovercraft the unique amphibious machine that it is. The 12000TD uses a low-pressure skirt to make the craft hover. The pressure underneath the hovercraft is only 2.5% higher than atmospheric pressure. The skirt is tapered from front to rear to improve seakeeping and each craft is fitted with an anti-spray apron to reduce spray.
Special tools are not required therefore fingers can be replaced without lifting the craft, saving time with routine maintenance. The skirt also uses the latest development in bag and finger design and is manufactured from materials proven during thousands of operating hours. Other modifications to the MkII variant of the craft include a change to the power output between propellers and lift fans plus a new form of “puff ports,” one on either side of the forward hull, to act as bow thrusters if required, although the variable pitch propellers make the craft highly manoeuvrable. These thrusters expel air from within the skirt when an internal valve is opened. The Operator requested a form of thruster to assist access to/from the craft boathouse as space is restricted. The small electric fan thrusters originally fitted to Hovertravel’s two Flyers on either side of the wheelhouse were eventually removed as surplus to requirements. A separate APU is fitted for the Air Conditioning system, which is digitally controlled to improve reliability. Each craft is designed to operate with just one engine to enable a return to a safe landing place.
The passenger cabin has four large windows on each side plus one smaller window forward on either side and two emergency escape doors on either side. The cabin’s maximum dimensions are 16m long, 5.8m wide and 2.5m high. The floor to ceiling clearance is 2m. The main cabin and engine bay cover superstructure is an aerodynamically designed composite panel structure fixed to a fully stressed aluminium frame. This design provides an extremely light-weight and rigid main cabin structure which is robust enough to endure years of commercial service. The cabin features 2 wheelchair spaces and 8 barrier-free seats to comply with Japan’s barrier-free (mobility) regulations. The seat layout is x2 wide (1.6m) along the outboard sides of the cabin and x4 wide (2.80m) through the centre of the cabin, 10 rows of seating in total. The walkway width between the banks of seats is 750mm. Seating is arranged to give each seat 2 possible means of escape from the craft.
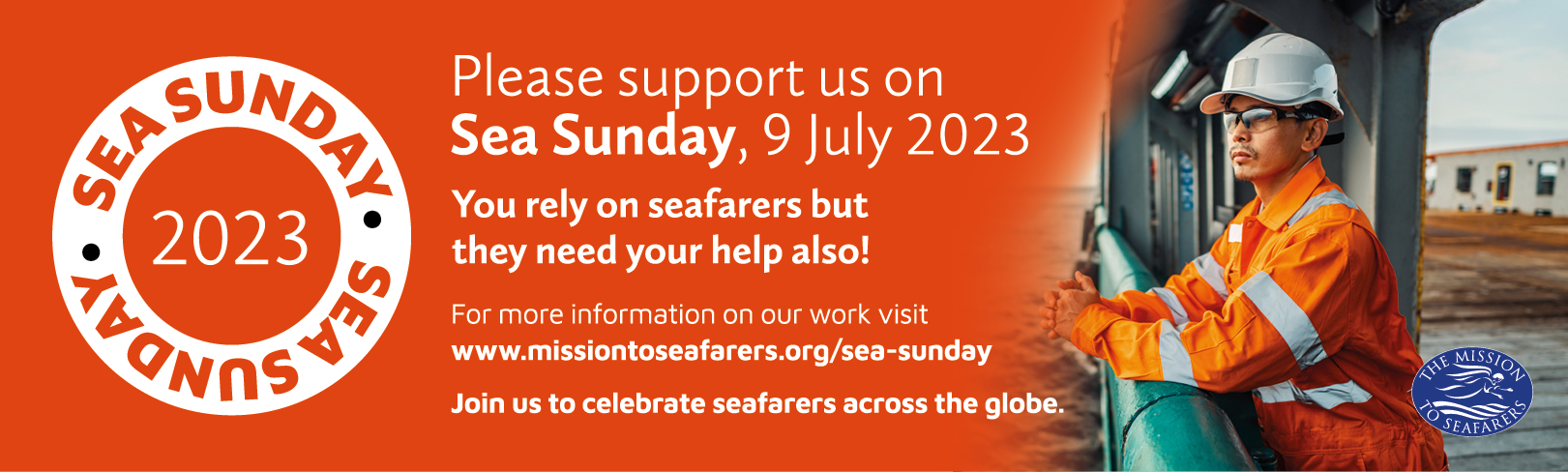
The storage/cargo area for passenger luggage and goods is located at the front of the cabin in the area beneath the wheelhouse (complete with roller shutter doors, as with the MkI craft) whilst passenger access (900mm wide) is provided via two electrically actuated over the bow loading ramps for quick and easy boarding of passengers and light cargo (again, as per the Hovertravel craft). There is a weathertight door at the front of the cabin across each of the access points. The centrally mounted wheelhouse provides excellent all-round visibility for the pilot, has electrically heated glass windows and is insulated against fire and noise. Three crew seats are provided here, and the navigation/communication equipment fitted consists of a Furuno FAR2218 Radar with 19” Display, Furuno GP3700 Chart Plotter, Furuno GP170 GPS, Furuno GS-100 Satellite Speed Log, Furuno FA-170 AIS and a Furuno FM8900-S VHF Radio.
From Solent to Pacific
The first newbuild for Japan emerged from Griffon Hoverwork Ltd. at Portchester for her maiden flight trials on 21st June 2023, proceeding over to the Hovertravel slipway at Ryde. This first craft was named Baien. All three craft are numbered, 01/02/03, and each has a unique livery. The Baien’s livery on the front of the cabin resembles a robot with the cockpit masquerading as the head. The craft names were announced by the Ōita Prefecture back on 7th February 2023, each being inspired by the names of three Edo-era scholars and educators called Bungo no Sanken. The names of the hovercraft were publicly solicited, and multiple proposals were received for each name. Governor Hirose commented that the names appeal to Ōita’s local characteristics both domestically and internationally and are easy for foreign visitors to remember. The Baien undertook around 100 hours of proving trials during her time at Ryde, being seen at various points between The Needles and Sandown Bay.
All too soon the Baien was loaded aboard the 11,522gt/2022-built heavy lift vessel BBC Sebastopol at Southampton’s Empress Dock on 14th July 2023 at the beginning of her delivery voyage to Japan. Upon arrival on 24th August at Ōita Ozai Public Port, the hovercraft was handed over after trials and made available for pilot training and trials across Beppu Bay between Ōita Airport in Kunisaki City and Ōita City. The craft made the 5,700-mile voyage from Southampton via Eemshaven in The Netherlands as hold cargo. Official handover came 3 weeks after arrival in Japan. The second craft, the Banri, touched water at Griffon Hoverwork’s Portchester base on 11th September and proceeded to Ryde the next day to begin a frantic week of trials and preparations as the 8,397gt/2000-built Grietje of SAL Heavy Lift collected her as deck cargo.
Each craft has four lifting points built into the hull, making lifting manoeuvres more straightforward. Due to the weather, the ship eventually sailed from Southampton after midnight on 20th September, bound for Ōita, Japan, via a call in Trapani, Italy. The ship also took shelter in Torbay for a short time after leaving the Solent. Other deck cargo on the voyage included two large mobile dockside cranes.
The Banri arrived safely in Ōita on 9th November and was announced as having been handed over on 16th November. Alas the Banri’s arrival coincided with a training mishap with the Baien on her first day of pilot training operations on 11th November. The starboard side of the craft came into contact with a 10m-15m area of concrete wall and guardrails on the hoverpads. The operator error caused damage to the starboard rudders, lift fan nacelle, skirt, and hull towards the stern of the craft. This was a setback to the operation with the Baien having to await recovery until the New Year with a team from Griffon Hoverwork attending. Hovercraft No.3, the Tanso, first departed from Portchester on 21st November and the port side engine decided that it wasn’t happy, so this was changed on 22nd November. The following day the craft returned to the building yard as scheduled for the completion of her internal fit-out and the application of the livery on the front of the cabin.
Flying the Flag
At around the time that the Tanso visited Ryde, another new Griffon Hovercraft was out and about, namely the 2000TD VCA Boreal, Hovercraft 503. This craft is for Traversiers (Société de Traversiers du Québec) of Canada and will join the 2012 built 2000TD AVC L’Esprit-de-Pakuashipi for use on the company’s Saint-Augustin-Pakua Shipi river crossing route.
The latter part of 2023 also saw the Polish Border Guard announce the signing of a contract for two Griffon Hoverwork 2000TD hovercraft for a patrol and intervention role conducted by Kashubian Border Guard Division in Stara Pasłęka, to be delivered in 2024. The hovercraft will be used in winter conditions on ice, in summer on water, and on water up to 20 nautical miles from the shore. The Wyvern, a new class of Landing Craft Air Cushion, was also announced by the company in September. Griffon Hoverwork continues to maintain the UK’s position as a world leader in hovercraft, with six decades of experience in naval architecture, design, development and construction.
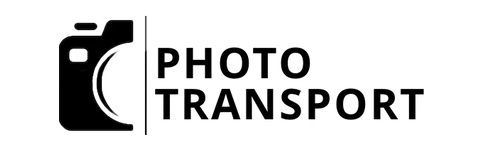
Comments
Sorry, comments are closed for this item