The world of tugs and towage is becoming ever more complex with a plethora of high-tech vessels now available for every conceivable combination of duties in pretty much any environment. Anyone who dismisses such vessels as “just a Tug” is greatly under estimating what these powerful little vessels are capable of. When flexing their muscles whilst working the largest of ships, the modern day tugs cannot fail to impress. The Damen Group is at the forefront of researching, designing and building this category of workhorse. Their latest product is the RSD Tug 2513, described as the ultimate ship-handling tool and the answer to the increasing scale of cargo vessels such as container ships. To keep pace with future demands, the new design redefines the concept of compact agility, optimised to operate in both direct and indirect towing modes. The prototype vessel was built at Damen’s ubiquitous Galati Shipyard on the River Danube in Romania that has a rich shipbuilding history dating back centuries. The yard was established in 1893 as Fernic Shipyard Galati and, by the end of 1970, the facility had built 477 vessels including barges, tankers, bulk carriers and tugs. The yard continued to thrive and, in 1994, the Damen Shipyards Group, already firmly established in The Netherlands and developing its international business, began co-operating with Galati by sub-contracting the building of cargo ship hulls to the yard. In 1999 the Damen Group, by then the yard’s biggest client, acquired Galati Shipyard and began streamlining and refining the organisation. Located on the banks of the River Danube and resembling a small city, the shipyard occupies a huge 45 hectare site and currently employs over 2,400 people directly. The very first RSD Tug 2513 had the Yard No. 515001 and was delivered to the Damen Group on 19th April 2018. Upon delivery the ground-breaking tug embarked upon a 25 port tour on 26th April, starting at Malta’s Grand Harbour. The vessel then visited ports in Italy (Trieste, Ravenna, Naples, Civitavecchia, La Spezia, Livorno and Genoa), France (Toulon, Bordeaux & Brest), Spain (Barcelona, Tarragona, Valencia, Algeciras and Bilbao), Morocco (Tanger) and Portugal (Lisbon). Upon leaving Brest the Innovation crossed to Southampton, arriving on 10th June for a 4 day stay via the western Solent. On 11th June the vessel was shown to members of the local shipping industry and media and the following day she visited Portsmouth. On 13th June a call at Solent Towage, Fawley, was made before continuing the tour eastwards to Dover, Felixstowe, Antwerp, Terneuzen Rotterdam, Ijmuiden, Delfzijl, Bremerhaven, Hamburg and Copenhagen where the tour was due to conclude on 29th July after an 8,500 mile adventure. The expedition was hailed as a success with one serious Buyer coming forward before the tug had even left Italy. The trip also generated a fascinating insight for her less familiar visitors into the specifics of how a state-of-the-art tug such as the Innovation actually functions. The tour was organised by Damen, through its subsidiary Damen Marine Services (DMS), which owns and operates the vessel. Once the tour was completed, the tug joined DMS’ fleet, available for charter.
Multi-Directional
As mentioned above, on a sunny 11th June it was Southampton’s turn to see the Innovation put through her paces. She was waiting for her dozen or so guests at Berth 48 in the eastern docks and what a fine sight she made. The RSD (Reverse Stern Drive) Tug 2513 draws on successful, reliable solutions from the Damen portfolio such as the ASD Tug 2411 and the ATD Tug 2412 series. Through a 5 year Research and Development process, the RSD Tug 2513 was developed with a strong emphasis on optimisation via computational fluid dynamics (CFD), notably with regards to directionally stable sailing behaviour in both directions. Extensive validation tests were performed at the Maritime Research Institute Netherlands (MARIN), which provided input for both the development of this vessel and for the further progression of Damen’s Virtual Towing Tank programme. So, the RSD concept was born, featuring the Damen patented asymmetrical Twin Fin (Skeg – first used on the Damen 2411 models) for true directional stability, combined with an increased amidships freeboard of 1 metre and a raised hull profile at each end of the vessel to cope with the significant forces generated (2.8m at the bow and 2.7m at the aft bow). The RSD 2513 has a smooth, rounded hull form and effectively possesses two bows, enabling the vessel to work equally well in either direction. The “always bow first” principle offers the flexibility for the vessel to operate optimally as both a bow and stern assisting tug whilst maintaining the safest position operationally. At the same time, the Twin Fin generates high towing performance at low engine power, resulting in low overall fuel consumption plus significantly improved manoeuvrability for ease of use in confined harbours. The operational range encompasses both exposed and sheltered coastal waters as well as ports of all types. The hull paint system consists of a tin-free anti-fouling with a 5-year lifespan.
Upon embarking the vessel the quality of finish was most impressive and she has a clean and uncluttered working deck. Everything is rounded to prevent corrosion and coated with epoxy paint whilst the deck surface is coated with anti-slip paint. The 1.1m bulwark also provides a safe environment for the crew to work in all conditions. Flush-mounted and integrated into the foredeck is a Damen Marine Components split-drum winch providing 31 ton pull up to 11m/min and a 175-ton brake load. The winch is combined with a solid, variable speed, high torque hydraulic drive system enabling the Master to haul and veer the towing line at the highest speed possible for the force applied. This equipment is full flame zinc coated with an epoxy paint system on top and features just two grease nipples. All rotating parts have a 5,000 hour working life. Ahead of the winch is a robust staple with a highly-polished stainless steel outward face. The type and number of winches (fore/aft) and propulsion types are flexible depending upon the Client’s needs. The superstructure is steel and on entering the accommodation from the main deck on the port side, the build quality continued to astound. The Chief Engineer’s cabin and a twin crew cabin are located on the port side of the superstructure with the remainder of the area occupied by the Galley, Mess Room and Captain’s cabin. Separating the Chief Engineer’s and Captain’s cabins is the stairway down to the machinery spaces. The layout is designed so that there is a non-residential compartment between each en-suite cabin to enhance privacy and minimise noise. The crew spaces are completely insulated, finished with durable modern linings, LED lighting and air conditioning.
Below the accommodation is the engine room, a surprisingly vast space that makes good use of the tug’s 13m beam. The presentation on board during the Southampton visit was made in the Mess Room but guests were informed that, had the numbers been greater, the presentation would have been relocated to the engine room! This sounded odd until we saw the space involved. The machinery space is both uncluttered and roomy. Located either side are the two MTU 16V 4000 M63L main engines. These units are 2,990mm long, 1,850mm wide and 2,070m high with a bore of 170mm and a 210mm stroke. Attached to the large drive shaft protruding from the rear of each engine is a Rolls-Royce US 255 360 degree azimuthing stern drive (ASD) unit with 2700mm diameter propellers in stainless steel ducts. The bollard pull/speed produced by this propulsion package is an impressive 75t/13 knots ahead and 70t/12.8 knots astern, thus demonstrating the bi-directional ability of the design. It must be said that the performance of the RSD 2513 is also remarkable considering the overall length is only 24.73m with an overall beam of 13.13m, 4.95m hull depth and 3.45m draught. Sited adjacent to each main engine is a Caterpillar C4.4 TA, 81 kVA, 400/230 V, 50 Hz generator set. At the forward end of the engine room are the fuel, hydraulic and bilge pumps whilst beyond a bulkhead are stores, workshop and switchboard room. Outboard of both main engines are the banks of box coolers for the closed fresh water cooling system, a proven method also to be found on all Damen tugs. This is designed for sea water temperatures of up to 35 degrees. Full control of the engine room is possible from the wheelhouse and main deck when the tug is carrying out an operation, so that the crew can monitor the alarms and analyse any problem in maximum safety. The RSD 2513 also has remote monitoring technology so that the machinery can be overseen from a shore based office rather than requiring a second Engineer aboard the tug. This will enhance preventative maintenance and ultimately reduce down time resulting from technical failures.
The space in the centre of the engine room can be occupied by the optional FIFI 1 fire fighting system with an output of 600m3/h, 1200m3/h or 2400m3/h. The superstructure-mounted monitor, when fitted, uses water or foam.
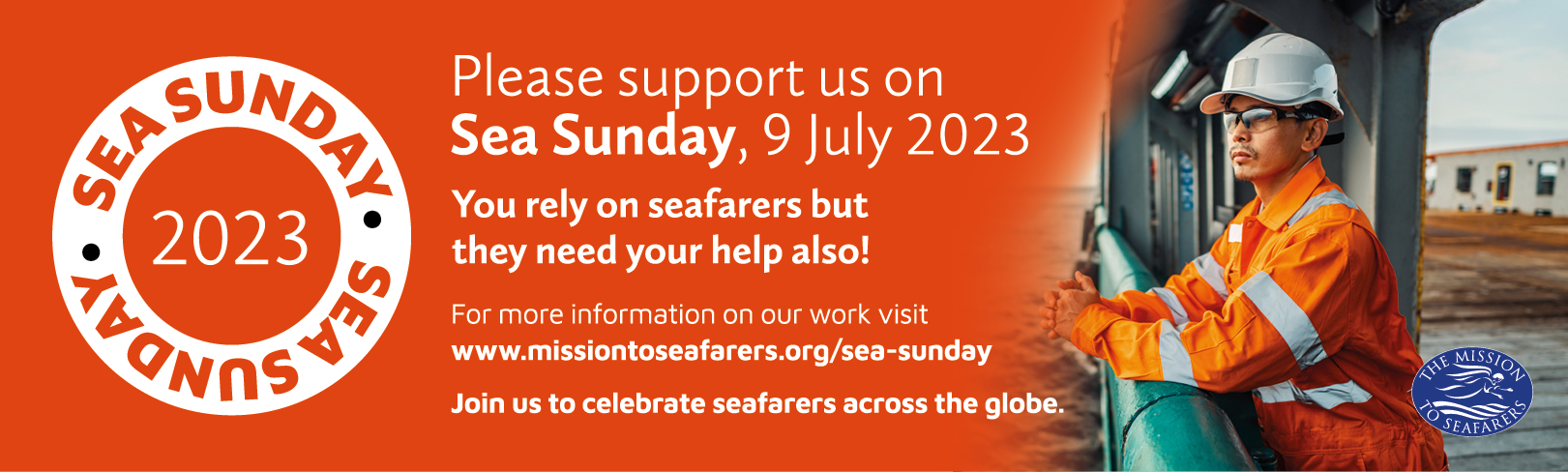
One deck above the living area is the Bridge Deck where the raised, 360 degree wheelhouse is located. This is glazed with Damen patented toughened safety glass that is glued to the framework to provide larger window areas and thus clearer lines of sight all around for the Master. The glass is shatterproof, similar to that used in cars, and represents a huge step forward in crew protection because the glass does not fragment when struck by a heavy object. The funnels are positioned abeam of the Master’s position on either side of the wheelhouse to minimise any obstruction to visibility.
The bridge control consoles are clean, ergonomic and minimalist with a digital dashboard and monitors located by the fore and aft control positions. The consoles are split with a central track-mounted seat for the Master running centrally between them linking the two control positions. The layout favours conventional bow operations, does not hinder the line of sight of the foredeck and the winch is controlled by two pedals, thus enabling simultaneous thruster and winch control. An integrated push-to-talk button next to the propulsion control connects to the VHF to maintain “hands on” operation. Other equipment includes electronic stability feedback technology. This assists in assessing the limits of the tug to ensure safe performance and is the first step towards the active stability system that Damen is developing. Atop the bridge is a lightweight and compact mast that has a folding option for close proximity working alongside large ships. The more central location of the wheelhouse also allows for pushing work under the flared bow of a large ship.
The RSD Tug 2513 offers extremely low levels of noise and vibration which comes courtesy of a flexibly mounted superstructure, engines and interior floors, 45 dB(A) silencers and double glazed windows with an argon filled gap acting as sound insulation. The Innovation is the first Damen tug to be equipped with resiliently-mounted/flexible glued accommodation. The huge benefit of this was demonstrated on the bridge deck during the trials. The difference between holding the handrail on the deck-mounted stairway and the adjacent handrail on the mounted deck housing was considerable. The wheelhouse also has a sound absorbing ceiling and floating floors.
Going Green – Literally
Whilst the 327gt Innovation was racking up the miles on her European tour a sister vessel was delivered from the same shipyard. Vessel No.2 is an IMO Tier III compliant version of the IMO Tier II compliant Innovation. To celebrate her green credentials the newbuild, handed over on 14th June, was christened Bis Viridis (above), translating as Double Green, with a paint scheme to match. The vessel has a modular Marine NOx Reduction System that makes her Tier III compliant. This Damen NOx system is an advanced active emissions control arrangement using SCR technology for NOx reductions up to emission standards according to IMO Tier III, suitable for marine diesel engines and fuels.
The project to produce a green variant of the RSD Tug 2513 has received funding from the European Union’s Horizon 2020 research and innovation programme under grant agreement No 636146. Upon delivery this second RSD Tug 2513 proceeded to Marseille to take part in ITS 2018 (the 25th International Tug Salvage & OSV Convention). At the time of writing the Bis Viridis (IMO 9842932) was en-route from Barcelona to Dunkerque with a final destination of Gorinchem. Unlike the Innovation, her green sister’s product specifications also list the option for a second set of Caterpillar C4.4 TA, 94 kVA, 440 V, 60 Hz generators. The Bis Viridis also has some revised wheelhouse features compared to the Innovation.
The RSD 2513 will be built as a stock vessel for almost immediate delivery to Buyers as well as custom built from scratch as orders arrive, subject to specific Customer requirements. There are plans for a smaller 20-23m version with a 60t bollard pull plus a larger variation has already passed the design stage. New tug models are being added to the Damen catalogue this summer in the form of the multipurpose ASD Tug 2312 and ASD Tug 2813. With a 60t and 80t bollard pull respectively, again both in push and pull mode, these vessels offer the ultimate mix of versatility and compactness by featuring smart layouts. The ASD Tug 2312 offers accommodation for six persons and a 54m2 aft deck area whilst the ASD Tug 2813 can accommodate 10 persons and has an 82m2 aft deck so both are suitable or escort and salvage duties. The harbour towage ASD 2810 has now been superseded by the ASD Tug 2811 and ASD Tug 3212 for port, coastal and exposed terminal operations with a bollard pull of 60t and 80t respectively, both in push and pull mode. Other projects underway include a CNG-E Tug in co-operation with Svitzer and MTU so the era of battery and natural gas powered tugs is coming over the horizon.
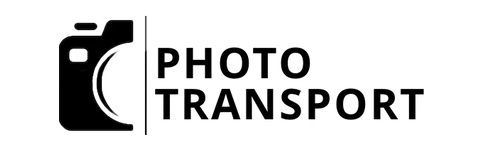
Special thanks must go to Ben Littler and Viktoria Adzhygyrei of Damen Group Communications for their invaluable assistance with information, diagrams and images, plus Chris Jones.
TECHNICAL SPECIFICATIONS
Owner | Damen Marine Services |
Flag | The Netherlands |
Port of Registry | Gorinchem |
Yard number | 515001 |
IMO | 9820623 |
Delivery Date | 19th April 2018 |
Basic Functions | Towing and Mooring |
Classification | Bureau Veritas I X HULL MACH Tug Coastal Service AUT UMS COMF-NOISE 3, COMF-VIB 3 |
Gross Tonnage | 327 |
Deadweight | 105 |
Length Overall | 24.73m |
Beam Overall | 13.13m |
Hull Depth at Sides | 4.95m |
Draught | 3.45m |
Draught Aft | 5.50m Incl. RSD units |
Displacement | 525t approx. |
Freeboard | 1,500mm |
Power Output | 4480bkW (6008bhp) @ 1800rpm |
Main Engines | 2x MTU 16V 4000 M63L |
Engine Manufacturer | MTU Friedrichshafen GmbH (Part of the Rolls Royce Group) |
Forced Ventilation | 60.000m3/h |
Generator Sets | 2x Caterpillar C4.4 TA, 81 kVA, 400/230 V, 50 Hz |
Thruster Propellers | 2x Rolls-Royce US 255, 700mm diameter |
Bollard Pull Ahead | 75t |
Bollard Pull Astern | 70t |
Speed Ahead | 13 knots |
Speed Astern | 12.8 knots |
Towing Winch | Hydraulically driven split drum 31 ton pull up to 11 m/min, reduced pull up to 38m/min, 175 ton brake |
Winch Brake Speed | 40m/min |
Anchor | 1x 360 kg Pool (High Holding Power) |
Anchor Winch | Electric 10 m/min |
Fendering | Cylinder + block bow fender, D-fender side/aft |
General Service Pumps | 2x Azcue CA 50/3A 20 m3/h at 2.35 bar |
Bilge Pump | Azcue CA 32/0.5 3.6 m3/h at 1.1 bar |
Fuel Pump | Azcue BR-41-10 12 m3/h at 1 bar Fuel |
Oil Purifier | 2x CJC, PTU3 3x FA/BLA 27/27, 1920 l/h each |
Cooling System | Closed box cooling system |
Hydraulic System | Main engine driven pumps |
TANK CAPACITIES |
|
Fuel Oil | 77.4m3 |
Fresh Water | 10.2m3 |
Bilge Water | 6.0m3 |
Sewage | 6.0m3 |
Dirty Oil | 2.5m3 |
Lubrication Oil | 2.5m3 |
Comments
Sorry, comments are closed for this item