The Marine Aggregates sector is a vital part of the shipping scene around the shores of the U.K, supplying the construction and highways industries with various grades of stone (shingle/ballast) and sand. A variety of dredging vessels perform these tasks in designated areas, bringing the dredged material ashore at ports such as Shoreham, Southampton, Portsmouth (a new cargo flow for the commercial port), Cowes, Poole and Dagenham.
New Generation
The 21st Century has welcomed a new era of dredger newbuilds that also feature economical and environmental characteristics which are now commonplace among new ships. Once again, Damen Shipyards Group has been at the forefront of bringing new designs to the table with their Marine Aggregate Dredger (MAD) 3500 and 5600 Trailing Suction Hopper Dredger (TSHD) variants. Damen developed this dedicated range of MAD vessels for the offshore mining of sand and gravel with particular attention paid to the optimisation of the hull design, which has resulted in the aggregate dredgers having excellent seakeeping performance. The enclosed bow of Damen’s offshore design shape ensures that these vessels can operate in harsh weather conditions, and protect their cargo from water ingress. Whilst similar in size to 20th century equivalents, the MAD 3500 is a completely new class that is said to represent a quantum leap forward in terms of both the quantity of product it can carry (20% more) and operational costs, thanks in part to the latest fuel-efficient propulsion systems and the ability to conduct operations while running on a single engine. During the process of finalising the MAD range, the design team at Damen sought input from experienced operators in the sector as well as from its own repair yards, which have been maintaining dredgers for many years, and its dredging mission equipment production subsidiary. The MAD 3500 is also designed to operate 24 hours a day, 7 days a week with just 9 crew. At any one time, dredging can take place with only two personnel on the bridge plus an engineer on duty. Unloading the entire vessel can be achieved in just 2-3 hours and is fully automated. The in-house designed trailing pipe, underwater dredge pump and screening towers ensure efficient dredging operations with an ability to also autonomously unload the dry cargo to shore and any port that can accept this size of vessel. The MAD series boasts several innovations to make operations safer and more efficient, resulting in the lowest cost per tonne of dredged material. The Damen designed draghead, underwater pump integrated with the trailing pipe and screening towers, plus two adjustable loading boxes, ensure efficient operations both at sea and in port.
A key part of the technology installed onboard the MAD 3500 is the modular screening tower which allows material brought up from the seabed to be sorted as it comes aboard rather than once it reaches land. This enables the vessel to retain only the grades of aggregate that are in demand while returning the rest to the seabed. The mooring system also sets a new standard, being designed around flow lines to ensure safe and efficient mooring at all times, whilst the addition of telescopic spud poles allows the MAD 3500 to hold position without the use of lines or the need for constant adjustment. As can be seen on each ship, the dredge pipes are situated above main deck level for safety, as well as easy inspection and crane reach, and the modular construction of the dredge systems ensures quick and easy replacement of worn parts of the piping and screening installation. This, in turn, is supported and enhanced by the use of Damen’s Triton remote-monitoring and analysis system that allows continuous optimisation and pre-emptive maintenance, which is achieved using ship-wide sensors to deliver operational data to both the bridge and managers onshore for real-time analysis. The hopper dredger is designed for mining marine aggregates at 55 metres below sea level. The submersed Damen dredge pump is directly driven by a continuous 1,400kW electric motor, i.e without a gearbox in between. Moreover, the electric motor forms an integral part of the trailing pipe structure. This air-filled motor is of the Permanent Magnet type and usually functions at 25 metres below sea level, approximately midway on the trailing suction pipe. Overall, the Damen MAD range has a dredging depth of up to 70m, a hopper capacity of 3,000-8,000 m3, a deadweight of 6,000-16,000 tonnes, a trailing pipe diameter of 700mm-900mm, a hull length of 90m-150m, a moulded beam of 16m-25m and a service speed of 11-15 knots.
The MAD 3500 Becomes Reality
On 19th December 2017 CEMEX UK Marine Limited signed a contract with Damen for the first Marine Aggregate Dredger (MAD) 3500 in Southampton. CEMEX UK is a leader in the building materials industry with over 3,000 employees, supplying aggregates, cement, concrete and other building solutions. The company had a pre-existing relationship with Damen, having utilised the service of Damen Shiprepair Amsterdam for maintenance of their vessels. The newbuild was named CEMEX Go Innovation and replaced the traditional 3,751gt/1990-built dredger Sand Heron. This once familiar ship at south coast ports was sold to Gulf Dredging & General of Shuwaikh Port, Kuwait City, Kuwait, in August 2021. The keel-laying for the CEMEX vessel took place in October 2018 at Damen Shipyards Mangalia, on the Black Sea coast of Romania, a facility that Damen had taken over the management of in July 2018 from Daewoo. The contract yard for Yard No. 563351 was Damen Shipyards Galati, Romania with the launch of the completed vessel taking place on 7th August 2019 at the Galati yard on the River Danube. Delivery for the vessel was stated as 15th December 2020 but ongoing trials and adjustments saw the vessel make her operational debut from Southampton and Shoreham in summer 2021 with the Writer managing to capture what was believed to be her first western Solent passage in service on 25th August 2021. To support the MAD 3500 dredgers and other Damen vessels, the shipbuilder established a service hub in the Port of Southampton, allowing the company to provide full, through-life support and to act as a repository of knowledge as well as critical components for these specialised vessels. With much of the existing North Sea fleet of aggregate dredgers due to be retired soon, many of which are based in the UK, Damen also hopes that the value of this new resource will grow over time as further MAD variants come onto the scene.
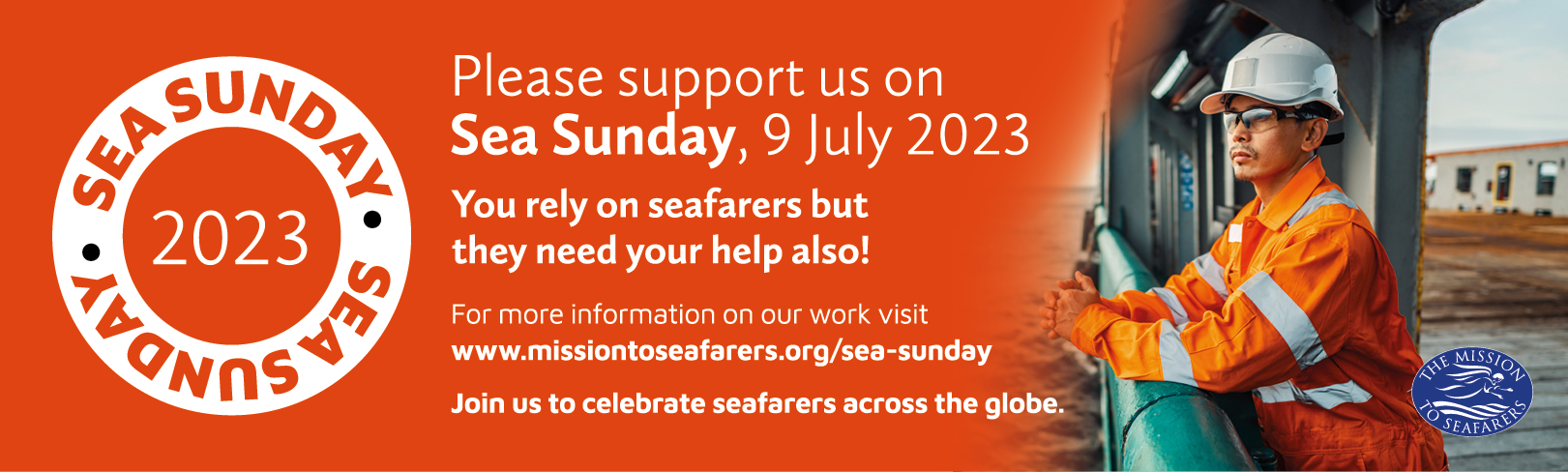
The CEMEX Go Innovation appeared to be hidden from view in terms of information concerning the newbuild, and likewise certain aspects of the MAD 3500 have not been disclosed, including a detailed General Arrangement diagram. Perhaps a certain degree of commercial sensitivity was involved as two competitors in the aggregates industry had ordered sister vessels. Anyway, whatever the reasons, as much information as possible was gleaned so as to complete this feature on what are now regular sights at south coast ports. A few months after the CEMEX contract, Hanson Aggregates Marine signed with Damen Shipyards Group on 10th May 2019 for the construction of a second MAD 3500 vessel. The Galati Shipyard was the venue for the construction of YN563352 with the keel being laid on 3rd October 2019 and the launch following on 17th September 2020. The dredge equipment and screening installation was constructed by Damen Dredging Equipment (DDE) in Nijkerk, The Netherlands. Galati has been associated with shipbuilding since the 1800s and, following the fall of the Communist regime the yard lost much of its financial support. The Damen Group first became involved with the yard in 1994 with full control of the facility following in 1999. Galați is the largest shipyard on the Danube, its output ranging from large tankers to small coast guard patrol boats.
The Damen Shipyards Group needs no introduction to regular readers of Newbuild of the Month, a global company offering a vast range of newbuild designs whilst its family routes remain firmly in The Netherlands, being founded in 1927 in Hardinxveld-Giessendam by Jan and Marinus Damen. This location is just 10km from the present-day headquarters. It goes without saying that Covid-19 did have an impact on the production of the vessel. Documentation gives the delivery of Hanson’s MAD 3500 newbuild as 5th November 2021 whilst Damen announced on 7th February 2022 that the vessel had completed her sea trials and had entered full revenue earning service in January 2022. Indeed, the new ship was noted at anchor at Saltmead Anchorage in the Solent off Thorness, Isle of Wight, on 26th December 2021 having just arrived on her delivery voyage. The Hanson Thames has been described as being based on the original MAD 3500 design, but benefits from the experience gained from the initial build of the series, the 4,919gt/2020-built CEMEX Go Innovation along with some adjustments to meet her own particular operational requirements, following Damen’s ethos of combining standardisation where possible with customisation where required. The Hanson Thames has the distinctive MAD 3500 TSHD profile with the high, enclosed bow form, deckhouse located forward with all dredge equipment surrounding the 3,500m3 capacity cargo hold (hence the design being known as the MAD 3500). Registered in Southampton, the 4,919gt Hanson Thames has a net tonnage of 1,475t, an approximate deadweight of 7,000t and an overall length of 103.50m. The extreme beam is 16.42m, the hull depth is 9.33m, the draught is 7.00m and the service speed is 12 knots. The dimensions of the MAD 3500 were essential to permit the use of the lock system at Shoreham Harbour in West Sussex, a regular call for dredgers on the South Coast. On 21st January 2022 the vessel made her first visit to the Port of London Authority’s Dagenham Terminal on the River Thames with a delivery of sand and gravel having started work for Hanson Aggregates Southeast. The 700mm diameter trailing suction system and draghead (which effectively acts as a giant vacuum cleaner) is located on the port side of the vessel and is lowered over the ship’s side hydraulically, to seabed depths of up to 55m. The material is pumped into the hold behind the superstructure. Two adjustable overflows are installed plus a modular fixed screening installation, with two loading chutes. The dry discharge system, manufactured by PLM Cranes BV and mounted on rails either side of the hold, consists of a clamshell with a 1,200m3/h average discharge capacity @ 1.75t/m3 dry material. As mentioned beforehand, two retractable spud poles are fitted into the hull to support the ship when unloading, negating the requirement for mooring lines. Aft on the starboard side is a hydraulically powered conveyor belt system. A high-capacity drainage system is also fitted to the working area with other systems including dredging indication software, a dredge control system, a dredge monitoring system, an automated dredge pump controller and a TSP automatic launch/recovery system. A telescopic boom deck crane is mounted on the dry unloader with a 6t capacity at a 20m outreach, capable of working over the entire vessel area. Options for the MAD 3500 include increased dredging depth, the aforementioned spud poles, bottom doors for the aggregates hold, the self-discharging system and IMO Tier III. The Hanson Thames is powered by two 6L26 Wartsila 6-cylinder diesel engines with a bore/stroke of 26.00cm/32.00cm @ 1000 rpm and a power output of 2,040kW per unit. Propulsion is provided by a pair of 2,800mm diameter controllable pitch propellers, CuNiAl-Bronze, in high efficiency nozzles. Manoeuvrability is assisted by two 1,265mm diameter transverse tunnel bow thrusters, 300 kW each, plus a pair of Fishtail 60° rudders. The general service speed is given as 12 knots, with a maximum of 14 knots. However, a service speed of 13.20 knots at a loaded draught of 6.60m is also given among the technical data. The machinery spaces below deck are located aft, with the funnel forming part of the deck furniture aft of the dry unloading system. The accommodation, located forward, covers 4 decks including the bridge, which also offers 360-degree visibility for navigation and dredging operations. The lower 3 decks house the crew accommodation (for a maximum of 14 persons) with 14 single cabins with private sanitary facilities. The Galley has dry/cold/freeze storage with capacity for 14 days plus there is also a waste area, changing room, laundry, contractor area, meeting room, office, messroom and a gym.
The Hanson Thames is understood to have had one or two teething issues as she beds herself into her year-round operation, but this is nothing unusual for a modern, high-tech ship. At the time of writing there were no details of a naming ceremony and enquiries to Hanson Aggregates had, sadly, not received a response. However, once again, sincere thanks go to Olena Tsukanova, Media Planner, Digital Platforms Support, Damen Shipyards Group.
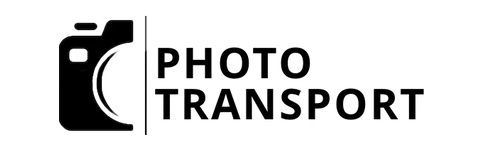
Comments
Sorry, comments are closed for this item