Various sectors of the maritime industry have evolved hybrid propulsion systems in recent years for use in a multitude of vessels. Some of these sectors, particularly the passenger and vehicle ferry categories, have gone one step further to develop all-electric powered vessels with (and sometimes without) conventional diesel engines as an emergency back-up. One of the most notable such newbuilds to date is the E-Ferry Ellen in Denmark. Perhaps a less likely sector of the shipping industry to rapidly develop an all-electric option was that of ocean-going ship handling/towage. However, as far back as 29th July 2019 Damen Shipbuilding signed a contract with Ports of Auckland, New Zealand, for a fully electric RSD-E Tug 2513 with full ship-handling capabilities and a bollard pull of 70 tonnes. The vessel was said to complete the green cycle of energy in the port with its unrivalled performance in sustainability. Damen’s RSD Tug 2513, unveiled in 2018, could already boast extreme green credentials, being fuel-efficient and IMO Tier III ready.
When the Ports of Auckland were looking to go a step further in terms of sustainable performance, they turned to Damen. The port had set itself the goal of being zero-emission by 2040 so a zero-emission option for the port tugs was one of the first steps, with the intention of making such a purchase initially explored in 2016. The port already had an example of the highly successful Damen ASD Tug 2411, and knew that Damen had been building hybrid tugs, so turning to the Dutch Shipbuilder was a logical choice for developing a fully electric model. Damen looked into the request and saw that it was technically possible. The next step was to consider the feasibility of full electrical operation from a business perspective. Data from the operational performance of the port’s ASD Tug 2411 allowed the battery requirements to be calculated for the proposed RSD-E Tug 2513.
Like Damen, Ports of Auckland and New Zealand as a nation are committed to sustainability. Already around 40% of primary energy generated in the country comes from renewable sources, including 80% of electricity, which comes primarily from hydropower and geothermal power. Damen Group was involved in every part of the design and build process for this pioneering project, the world’s first all-electric ship handling tug. The work included equipment such as the charging station, which is based on technology that has already demonstrated its credentials in the automotive industry. A simple system, it features four cables on the vessel being connected to the station. Once connected, the 1.5MW charger takes just two hours to fully charge RSD-E Tug 2513. The tug design also has high levels of redundancy in its power systems. The electrical system has built-in redundancy, with the batteries arranged in strings so if one battery in a string fails, the others simply carry on the work.
To ensure absolute safety, the electric tug also features a pair of 1,000KW generator sets, which provide enough power for the tug to operate at a bollard pull of 40 tonnes in the event of an electrical system failure, or if the vessel needs to operate beyond the battery capacity. However, the propulsion system is not hybrid. In normal operation, the generators are not used as the vessel and her battery system has been designed to meet the port’s normal operational needs.
After partnering with Echandia in 2018 to build the world’s first electric passenger ferry fleet in Copenhagen, Damen Shipyards again collaborated with the company in 2020 in creating another landmark of maritime transportation, the electric tug. The vessel is anticipated to have a 25-year life span and will save approximately 465 tonnes of CO2 in diesel emissions annually. The newbuild is powered by the Echandia E-TUG energy storage system (ESS) which is based on the Toshiba SCiBTM LTO cells. With their exceptional safety rating, supercharging capability, long life span and relatively light weight, the LTO battery racks, 80 of which are installed on the tug (representing 2,784 KWH of power), will allow the specified 70 tonne bollard pull on a single charge with two ships being handled before a recharge is needed.
One Ground-Breaking Design from Another
The RSD Tug 2513 is the tug that the all-electric version is based upon and was described when completed as the ultimate ship-handling tool and the answer to the increasing scale of cargo vessels such as container ships. The RSD (Reverse Stern Drive) Tug 2513 was spawned from successful, reliable solutions from the Damen portfolio such as the ASD Tug 2411 and the ATD Tug 2412 series. Through a 5-year Research and Development process, the RSD Tug 2513 was developed with a strong emphasis on optimisation via computational fluid dynamics (CFD), notably with regards to directionally stable sailing behaviour in both directions. Extensive validation tests were performed at the Maritime Research Institute Netherlands (MARIN), which provided input for both the development of this vessel and for the further progression of Damen’s Virtual Towing Tank programme. So, the RSD concept was born, featuring the Damen patented asymmetrical Twin Fin (Skeg, first used on the Damen 2411 models) for true directional stability, combined with an increased amidships freeboard of 1 metre and a raised hull profile at each end of the vessel to cope with the significant forces generated (2.8m at the bow and 2.7m at the aft bow). The RSD 2513 has a smooth, rounded hull form and effectively possesses two bows, enabling the vessel to work equally well in either direction. The “always bow first” principle offers the flexibility for the vessel to operate optimally as both a bow and stern assisting tug whilst maintaining the safest position operationally. At the same time, the Twin Fin generates high towing performance at low engine power, resulting in low overall power consumption plus significantly improved manoeuvrability for ease of use in confined harbours. The operational range encompasses both exposed and sheltered coastal waters as well as ports of all types. The first RSD Tug 2513 was the 327gt/2018-built Innovation, built at the Damen Galati Shipyard on the River Danube in Romania. Vessel No.2 was an IMO Tier III compliant version of her IMO Tier II compliant sister and, to celebrate her green credentials, this tug, handed over on 14th June 2018, was christened Bis Viridis, translating as Double Green, with a paint scheme to match. The vessel had a modular Marine NOx Reduction System that made her Tier III compliant. This Damen NOx system was an advanced active emissions control arrangement using SCR technology for NOx reductions up to emission standards according to IMO Tier III, suitable for marine diesel engines and fuels. The project to produce a green variant of the RSD Tug 2513 received funding from the European Union’s Horizon 2020 research and innovation programme. The very first RSD-E Tug 2513, which features over 80 changes compared to the original specification due to the electric power source, was built by Damen Shipyards at their Song Cam Shipyard in Haiphong, Vietnam. This facility opened on 20th March 2014 with a ceremony involving the then Vietnamese Vice-Minister of Transport, Mr Nguyen Hong Truong, who cut the ribbon at the latest addition to Damen Shipyard Group’s portfolio.
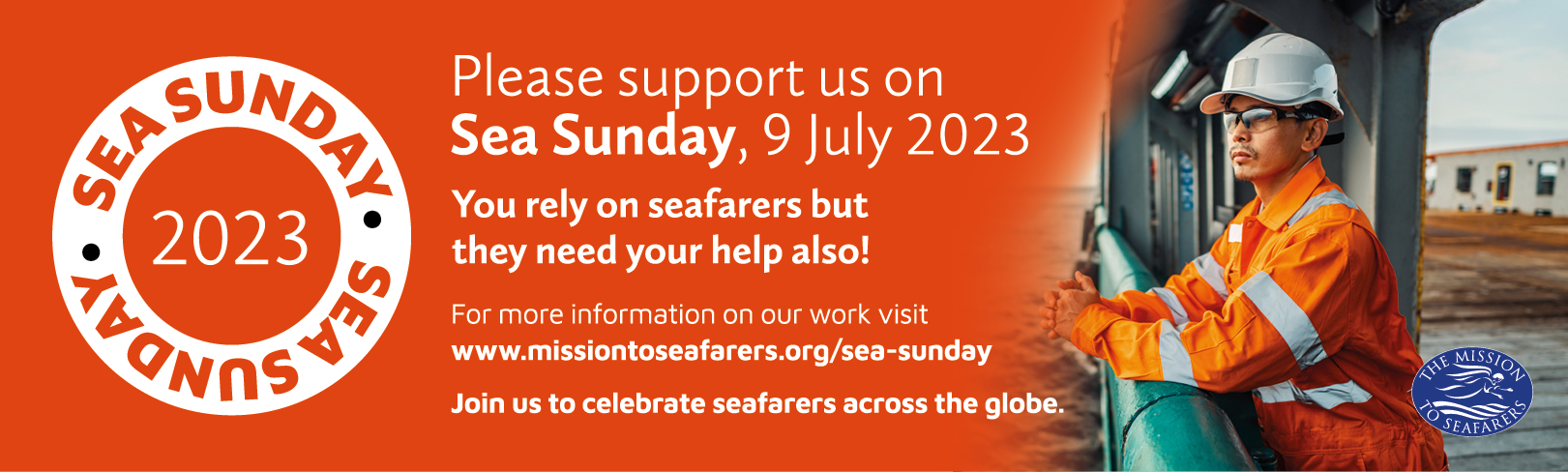
Damen Song Cam is considered state-of-the-art, bringing a western shipyard designed to meet European health, safety and environmental standards into a Vietnamese environment. Damen already had a well-established history in Vietnam (226 newbuild vessels), working with 5 shipyards for more than 12 years prior to the construction of the Song Cam yard.
With direct access to open sea, the yard began life on a 43-hectare site, of which 500m was directly alongside the River Cam. The yard has a 120m long and 85m wide outfitting hall, plus extensive paint and carpentry workshops. Damen Song Cam is set to become the largest series producer in the Group so everything revolved around efficiency from the outset. The shipbuilding hall is a dedicated facility with 3 overhead cranes of 25 tonnes each over each bay. Around 300 people worked at the shipyard initially, rising slowly to 800 at the end of phase 1, enabling the yard to handle 40 vessels annually. After that, phase 2 and 3 brought extra facilities, making the yard suitable for building up to 50 hulls and outfitting a further 80 vessels annually.
The maximum workforce was expected to be around 2,500 people. The new Owner of the RSD-E Tug 2513, Ports of Auckland, can trace its roots back to the 1850s when the first Queen Street wharf was constructed. The Auckland Harbour Board was established in 1871 to administer the port by an Act of Parliament with some of the present-day infrastructure beginning to appear from 1906. The Fergusson Container Terminal was built in 1971 and the first container ship, the Columbus New Zealand, called on 23rd June 1971, five weeks before the Writer was born! Ports of Auckland was formed in 1988, purchasing the Auckland Harbour Board’s land assets. In 2005 Ports of Auckland delisted from the New Zealand Stock Exchange and the company is now owned wholly by Auckland Council’s investment arm (Auckland Council Investments).
Amp-le Proportions
The 353gt E-tug has a length overall of 24.73m, an overall beam of 13.13m, a hull depth of 4.95m at the sides and a minimum draught of 3.65m. The vessel’s layout features three main levels. Within the deckhouse, the Chief Engineer’s cabin and a twin crew cabin are located on the port side aft at Main Deck level with the remainder of the area on that side occupied by the Galley and Mess Room. On the starboard side there is the captain’s cabin and another cabin for two crewmembers. Located centrally in the forward area of this accommodation, and separating the Mess Room and a twin cabin, is the stairway down to the machinery spaces. Slightly aft and adjacent to this access is the stairway to the wheelhouse. The layout is designed so that there is a non-residential compartment between each en-suite cabin to enhance privacy and minimise noise. The crew spaces are completely insulated, finished with durable modern linings, LED lighting and air conditioning. The Below Main Deck level, beneath the accommodation, is the spacious engine room, which makes good use of the tug’s 13m beam. This area is uncluttered and located on either side are the two C32TA, 1175 kVA, 690 V, 60 Hz main engines (generators). These V12 units are 1,874mm long, 1,600mm wide, 1,369mm high and weigh 3,005kg (dry weight). The bore is 144mm, the stroke is 162mm and the displacement is 49,756mm2. Situated midships are the pumps. Aft of this space is the propeller room that contains the two Azimuth Reverse Stern Drive (RSD) 3m diameter Kongsberg Maritime US 255 L-Drive units. These units are driven by a pair of TW 1400R-L electric motors, manufactured by Ramme Electric Machines GmbH of Germany. Forward of the engine room is the switch board room, and forward of that in the bow is the battery room. The latter contains the aforementioned Echandia E-TUG energy storage system that features a total of 80 Toshiba SCiBTM LTO racks. These contain 2,240 batteries overall and, for redundancy purposes, are arranged in strings. If one battery in a string were to fail, the others would simply carry on the work. The tug’s power output is 3,700bkW at 500rpm and this produces an ahead bollard pull of 70.90 t, an astern bollard pull of 70.50 tonnes and a speed ahead/astern of 12.30/11.80 knots. Outboard of both main engines, are the banks of box coolers for the closed fresh water-cooling system, a proven method also to be found on all Damen tugs. This system is designed for sea water temperatures of up to 35 degrees. Full control of the engine room is possible from the wheelhouse and main deck when the tug is carrying out an operation, so that the crew can monitor the alarms and analyse any problem in maximum safety. The RSD 2513 series also has remote monitoring technology so that the machinery can be overseen from a shore-based office rather than requiring a second Engineer aboard the tug. This will enhance preventative maintenance and ultimately reduce down time resulting from technical failures. One deck above the living area is the Bridge Deck where the raised, 360-degree wheelhouse is located. This is glazed with Damen patented toughened safety glass that is glued to the framework to provide larger window areas and thus clearer lines of sight all around for the Master. The glass is shatterproof, similar to that used in cars, and represents a huge step forward in crew protection because the glass does not fragment when struck by a heavy object. The exhausts are positioned abeam of the Master’s position on the port side of the wheelhouse with minimal obstruction to visibility. The bridge control consoles are clean, ergonomic and minimalist with a digital dashboard and monitors located by the fore and aft control positions. The consoles are split with a central track-mounted seat for the Master running centrally between them linking the two control positions. The layout favours conventional bow operations, does not hinder the line of sight of the foredeck and the winch is controlled by two pedals, thus enabling simultaneous thruster and winch control. An integrated push-to-talk button next to the propulsion control connects to the VHF to maintain “hands on” operation. Atop the bridge is a lightweight and compact mast that has a folding option for close proximity working alongside large ships. The more central location of the wheelhouse also allows for pushing work under the flared bow of a large ship.
Name that Tug
On 28th May 2020 members of the public were invited to suggest names for the Ports of Auckland’s new electric tug, with the chance of winning $1,000 and a ride on the vessel. Entries closed on 3rd June 2020 when a shortlist was drawn up of the most popular suggestions, ensuring they were appropriate, fit for purpose and could easily be understood over the marine radio by ship’s crews. Very wisely, Ports of Auckland reserved the right to name the tug the name suggested by the winner but was not obliged to do so. The shortlist of names was, Ārahi (meaning to lead, escort, conduct, drive); E.T. (short for Electric Tug), Hiko (meaning electrical, power, electronic, electric, lightning) and Sparky (diminutive of spark, slang for an electrician, related to electricity, but also sparking change).
On 17th June 2020 the tug’s name was chosen as Sparky with a “Helen from Auckland” winning the prizes after being one of those who suggested the winning name. Having been handed over by the shipyard on 18th April 2022, the Sparky departed from her birthplace on 19th April, reaching her new home on the morning of 7th June when Ports of Auckland welcomed the world’s first full-sized ship-handling electric tug, in the Waitematā Harbour. The delivery voyage was made using the back-up
Caterpillar C32TA diesel generators. The welcome party featured the port’s other tugs. Preparation and crew training followed. The christening ceremony for Sparky was originally planned for 25th July but, at the time of writing, the event was being rescheduled for August. Sparky’s godmother was Marama Royal, the Chair of Ngāti Whātua Ōrākei, the port’s local iwi. Marama also gave Sparky a name in te reo (Māori language) and this is Tiaki, which means to care for people and places. The ceremony was held on Captain Cook Wharf at the Ports of Auckland. The Sparky was also in pride of place out on the water on 12th August welcoming the first cruise ship back into Auckland after a 2-year hiatus. Ports of Auckland took a bold step in pioneering the use of fully electric harbour tugs and, where they lead, others will follow, and indeed are. At the time if writing, the Damen Song Cam Shipyard was building two more examples of the RSD-E Tug 2513.
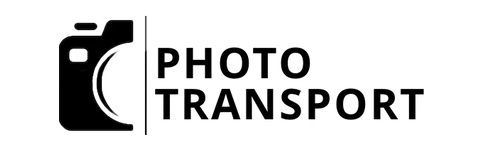
Comments
Sorry, comments are closed for this item