The plethora of Offshore Services related vessels continues to grow despite the stagnation and even constriction of the industry since the fall in oil prices. Vessels are being laid up and previously buoyant companies are fighting for survival, but the industry as a whole marches on. Having more than one string to your bow helps tremendously so the multipurpose vessels have a better chance of maintaining employment around the globe. One such newbuild was delivered on 29th August 2016 to Harvey Gulf International Marine, LLC of New Orleans, Louisiana, U.S.A. Built as Hull No. 234 by Eastern Shipbuilding Group, Inc., the Harvey Stone is a RAmpage 6500-ZH hybrid Multi- Purpose Field Support Vessel (MPFSV), designed by Robert Allan Ltd. of Vancouver, B.C. The same shipyard was also completing MPSVs Harvey Sub-Sea (delivery 2016) and Harvey Blue-Sea (delivery 2017) from a design provided by VARD Marine. Founded in 1955, Harvey Gulf International Marine is a marine transportation company that specialises in towing drilling rigs and providing offshore supply and multi-purpose support vessels for deep-water operations in the U.S. Gulf of Mexico. In December the company website displayed a fleet of 57 PSVs (Platform Support Vessels), 3 MPSVs (Multipurpose Support Vessels) and 5 FSVs (Fast Support & Utilty Vessels). This total included vessels under construction. The latest MPFSV was not shown in this total, suggesting the information was outdated. Harvey Gulf can trace its history back to 1955 when Captain Numa J. Guidry assembled a fleet of inland towing vessels to service the Gulf Coast transportation market and called his company Harvey Canal Towing Company. Ten years later, Captain Numa’s two sons joined the family enterprise and helped expand the company into the offshore ocean towing and rig moving industry. The company’s name was changed to reflect the new direction: Harvey Gulf International Marine, Inc. From the early 1960’s to the late 1990’s, Harvey Gulf maintained and operated a fleet of both offshore, and inland towing vessels that towed, among other things, jack-up and semi-submersible drilling rigs, bulk cargo barges, and large structures and facilities loaded on barges. The company also regularly towed liquefied natural gas (propane) filled barges from Louisiana to ports in the Caribbean, U.S. East Coast and U.S. Gulf of Mexico. In 1988, Shane J. Guidry became the third generation of the Guidry family to run the family business and became President and CEO in 1997. As the years progressed, Harvey Gulf transitioned from a full-service towing operator to one specialising in offshore towing in the Gulf of Mexico. As part of this specialisation, Harvey Gulf divested the company’s liquefied petroleum gas division, sold all of its inland towing vessels and replaced them with larger, more powerful offshore towing vessels. From 2003 the ongoing fleet expansion included Offshore Supply Vessels. On 21st August 2008, Mr. Guidry, along with The Jordan Company, L.P., a New York based private equity firm, acquired Harvey Gulf from the Guidry family with Mr. Guidry remaining as Chief Executive Officer. In 2015 the first of six dual fuelled LNG powered OSVs was delivered in the form of the 4,458gt Harvey Energy. These vessels became the first to use LNG as a fuel in the U.S.A and all achieved “ENVIRO+, Green Passport” Certification by the ABS, which made them the most environmental friendly OSVs in the Gulf of Mexico.
First in Class
The 2,343gt Harvey Stone is the first RAmpage 6500-ZH MPFSV and belongs to the Robert Allan Ltd. (RAL) RAmpage series of offshore support tugs developed to address a gap in the market for smaller high-performance towing and anchor-handling tugs for critical offshore terminal and oil-field duties. These tugs are designed to be able to maintain station in extreme ocean conditions with enhanced manoeuvring and sea-keeping capabilities. RAL was founded in 1930 when Robert Allan commenced private practice as a consulting Naval Architect after serving as Technical Manager of a local major shipyard. A 1907 graduate naval architect from the University of Glasgow, he was responsible for numerous enduring designs produced for the growing British Columbia fishing fleet and coastal ferry services, among others. His reputation for quality designs was enhanced by the notable, classic ocean-going motor yachts Meander (1934) and Fifer (1939), both of which are still in active service on the Pacific Coast. Robert F. (Bob) Allan joined his father in the practice in 1945. The business grew steadily and was instrumental in the development of specialised tugs and barges for the forestry and mining industries along the B.C. coast etc. Incorporated as Robert Allan Ltd. in 1962, the company continued to expand and achieved international recognition for the high standards and performance of its many unique and specialised designs. In 1973, Robert G. (Rob) Allan joined the company, following the family tradition. In 1981 he succeeded his father as President, leading the company into a new generation of computer- based design technology. The expanding firm created a wide range of distinctive designs including modern high-performance ship-assist and escort tugs, icebreakers, government service vessels, and high speed craft. The shipyard at which the Harvey Stone was built, Eastern Shipbuilding Group, Inc., was originally established in 1976 for the purpose of constructing commercial fishing boats for the company’s founder and President, Brian R. D’Isernia. In 1981, the yard’s diversification began with the delivery of the first Offshore Supply Vessels. Today, Eastern’s history includes a diverse portfolio of over 350 vessels including ferries, OCVs, highspeed craft and dredgers. The steel for the newbuild was cut on 31st December 2014 and the keel was laid on 13th January 2015. Launch day followed on 18th December 2015 with delivery taking place in August 2016 as mentioned above. The Harvey Stone will serve as a dedicated field support vessel for the Shell Stones Floating Production, Storage and Offloading (FPSO) offshore terminal, hence her name Harvey Stone, linking her Owners and her place of work. An FPSO unit is a floating vessel used by the offshore oil and gas industry for the production and processing of hydrocarbons, and for the storage of oil until it can be offloaded onto a tanker. FPSOs are preferred in frontier offshore regions as they are easy to install, and do not require a local pipeline infrastructure to export oil. FPSOs can be a conversion of an oil tanker or can be a vessel built specially for the application.
Ready for Anything
The primary duties of the 64.80m long and 18m beam vessel will be to operate as the dedicated pull-back tug, in support of, and assisting the berthing, loading and departure of shuttle tankers of up to 46,287dwt at the FPSO site. The Harvey Stone also has a maximum draught of 5.50m, a moulded hull depth of 7.80m and a navigational draught of 6.40m. Ship-handling fenders at the bow comprise an upper course of 900mm diameter cylindrical fenders and a lower course of 450mm thick “W” block fenders. A 350mm x 350mm hollow “square” fender provides protection along the main deck sheer line and 450mm thick “W” block type fendering is used at the stern. The Harvey Stone is the first RAmpage series vessel to have the sponsoned hull form, similar to the RAstar escort series tugs. This allows the vessel to perform in the following sea states:
Berthing operations – Winds up to 15 m/sec. (30 knots), significant wave heights up to 2.5m and current speeds up to 1.1 m/sec. (2 knots).
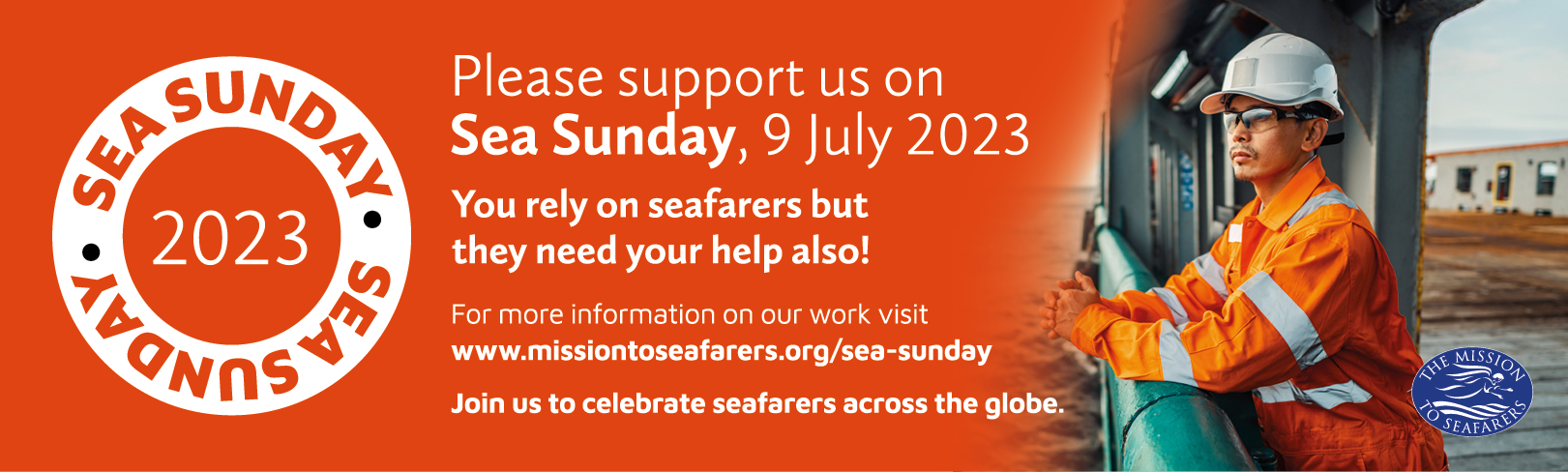
Shuttle Tanker Pull Back Operations – Winds up to 20 m/sec. (40 knots), significant wave heights up to 3.0m and current speeds up to 1.1 m/sec. (2 knots).
Other duties include evacuation assistance in accordance with the Gulf of Mexico Emergency Evacuation Plan (EEP), i.e. escorting the FPSO in the event of disconnection from the submerged buoy mooring for hurricane avoidance purposes. A total of 120 survivors (in addition to the 15 crewmembers, or maximum of 24) can be accommodated in the event of an emergency. Special attention was paid to the overall design in order to meet the HAB+ noise and vibration requirements, including vibration isolation of the main engines and silencers, and a specialised flooring system. To ensure the standards were met, Eastern Shipbuilding commissioned a separate noise study (including an FEA model of the hull) by Noise Control Engineering. The large main forward mounted deckhouse contains a spacious galley, mess rooms for Officers and crew, cabins for Senior Officers, HVAC room, lockers, etc. The lower deck contains galley stores, cold storages, laundry room, engineer stores, workshop, crew cabins etc. With forward and aft control stations, the wheelhouse has maximum all-round visibility particularly to both fore and aft deck working areas. The MPFSV is also equipped to tow the FPSO in case of mechanical breakdown at any time during the transit from or to the oil field. The deck machinery includes a single drum hawser winch at the bow, a water-fall double drum towing winch at the stern, stern roller, shark’s jaw-top pin unit, gobeye, tow hook, tugger winches, capstans, storage reel, etc. The maximum bollard pull for the vessel is 106t. The maintaining and inspection of the floating hose on site is also undertaken plus the transportation of stores and general cargo to the FPSO (including containerised stores and equipment, bulk stores, fuel and potable water). Such freight is carried on the 250m2 aft cargo deck with a deckload in excess of 5 tonnes/m2. The cargo deck is equipped with a MacGregor 10 Ton Hydraulic Knuckle Boom Crane with a 10t safe working load (SWL) at an outreach of 15m and an SWL of 20t at an outreach of 8m. The crane itself weighs 50t and is driven by two 165Kw motors. The hook travel is 1500m and two hoisting speeds are available. The Harvey Stone can maintain station via the installed Dynamic Positioning 2 (DP2) system, a FFV2 firefighting system is fitted and she can also perform some anchor handling duties. The standard fuel capacity is 234.5m3 but a maximum of 874m3 can be carried to enable extended endurance at sea. Likewise in endurance mode the vessel can also carry 192m3 of fresh water, 94m3 of firefighting foam and 1,496m3 of ballast/drill water. The hull is fabricated from Ordinary Strength Steel, ABS Grade A with High Strength Steel, ABS Grade AH36 used for the crane pedestal, winch underdeck girders, beams etc. A double-hull is essential, which segregates all fuel, oil, and sewage from the hull as required by the specification and due to the available fuel capacity.
Eco-Equipped
The 1,589 dwt vessel is fitted with a hybrid propulsion system that provides economic propulsion (eco-transit speed is 8-9 knots) and station keeping on one engine, driving machinery and providing electrical power to the propulsion units and/or bow thrusters. The hybrid system has a dual output (PTO/PTI)/single input gearbox driving the propulsion shaft line on one side and the engine/generator on the other. Since the vessel will see a large percentage of time in standby mode while on station, it is more economical to utilise a single main engine to drive all propulsion units and systems. The arrangement is configured to operate a standard vessel with electrical power being generated via shaft alternators in conventional mode or DP mode.
The Harvey Stone is powered by a pair of General Electric 12V250 MDC main engines with EPA Tier 4 emission certification, each rated 3,495kW at 1,000 rpm. This vessel design is in fact one of the first applications of an EPA Tier 4 GE 12V250MDC power unit. The cylinder bore of a 12-cylinder 12V250MDC unit is 250mm, the maximum continuous rating is 3500 kW and the piston stroke is 320mm. These engines drive two Schottel SRP 3030CP azimuth thrusters with 3,400mm diameter controllable pitch propellers via a Reintjes LAF 3414 single input with dual outputs gearbox. The service speed produced is 13-14 knots. For manoeuvring, a pair if 610kW Schottel STT tunnel thrusters are installed and these also provide the DP-2 capability in conjunction with the azimuth thrusters. The ship’s electrical power generation and hybrid system is provided by Robichaux Automation and Control Inc., with primary propulsion load feed to a VACON DC-Grid main propulsion switchboard. Onboard power generation is provided by two 350kW/1800rpm Cummins HCM534D1 Tier 3 generators and two Marelli Shaft Motor/Generator units each with 1,000 kW of power. Emergency electrical power is sourced from a single 120kW/1800rpm Cummins QSB7-DM Tier 3 generator. The vessel is fitted with a FFS off-ship firefighting system to Class FFV 2 system requirements, which calls for a significantly higher firefighting capacity than a standard FFV1 vessel.
Field Trip
The Harvey Stone is now at work on the Shell Stones field which is situated in Block 508 in the Walker Ridge area of the Gulf of Mexico, around 322km off the coast of New Orleans, Louisiana, U.S.A. The ultra-deepwater project lies in a depth of approximately 2,900m. The field is owned and operated by Royal Dutch Shell. The Stones field is estimated to hold more than two billion barrels of oil equivalent (boe). Production on site was achieved in September 2016 and it hosts the deepest FPSO installation in the world. Situated near the St. Malo, Cascade and Chinook developments, the Stones field was actually discovered in 2005. The Stones-2 well was drilled in 2005 to a depth of 8,705m. The Stones-3 exploration well was drilled in 2008 and reasserted the multiple oil-bearing sands. Shell made the decision to invest in the field development project in May 2013. The first phase of development includes two subsea wells tied back to the FPSO vessel that the Harvey Stone services. Six more development wells will subsequently come on stream, raising the production capacity of the field. The first phase of development is expected to reach a peak production capacity of 50,000boe/day by the end of 2017 from more than 250,000boe of recoverable reserves. The FPSO used is a converted Suezmax tanker. It is secured using buoyant turret mooring (BTM) technology. The detachable buoy equipped turret enables the vessel to vane on location or disconnect from the well in the event of adverse weather. The steel lazy wave risers linking the subsea systems to the BTM are being used for the first time with a separable FPSO. The FPSO vessel has the capacity to process oil at a rate of 60,000 barrels a day and gas at a rate of 15 million standard cubic feet a day. The Suezmax hull can store approximately 800,000 barrels of crude oil.
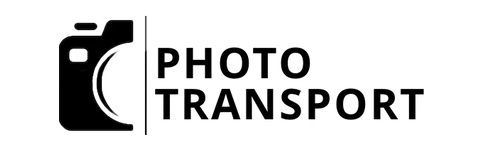
Comments
Sorry, comments are closed for this item