In days gone by ships engaged in the offshore trade were frequently adapted from a pre-existing vessel ranging from a deep sea trawler to an anchor handling vessel or larger. However, with the progression of operator requirements and technology to name but two factors the oceans are playing host to an increasing number of impressive working ships bristling with gadgetry. Of course the innovations do not stop with the equipment carried by these workhorses but also encompass the design of the ships themselves.
The subject of this feature is the 12,983gt and 130 metre long Island Performer built for Island Offshore X KS of Ulsteinvik, Norway. Launched on 16th April 2014 and delivered on 8th July 2014 the ship is a Riserless Light Well Intervention/Inspection, Maintenance and Repair vessel complete with the unmistakable X-BOW® hull form.
X-ceptional Design
Ulsteinvik is the commercial and administrative centre of the municipality of Ulstein in Møre og Romsdal county in Norway. The town is located on the west side of the island of Hareidlandet, approximately 23 kilometres southwest of the city of Ålesund. Island Offshore is based here as is one of the most innovative shipbuilders of the modern age, the Ulstein Group. Perhaps it is no coincidence that the ship owner should select Ulstein to build their latest ship but the ship design and construction group has been in operation for 97 years having been founded by Martin Ulstein in 1917. Nowadays the company is run by his grandchildren, with Gunvor Ulstein as CEO. The Ulstein shipyard has sold over 50 X-BOW® ships since the company started to develop Ulstein designs in 1999. These ships are of different types including PSVs, anchor handling tug supply vessels, seismic vessels and construction and well stimulation vessels. They work in all weathers and have been a resounding success. Bourbon Offshore Norway believed in the new bow concept from the outset when the initial drawings were released and worked closely with Ulstein on the development of the first ship. The prototype was created as an AX104 series anchor handling tug supply vessel (AHTS) launched in 2005.
Delivered in 2006, she was christened Bourbon Orca and subsequently received a number of awards, including the Norwegian Design Council’s design award, the Engineering Feat of the Year, and Offshore Support Journal’s and Skipsrevyen’s “Ship of the Year” Awards. Other vessels of the same design have since received similar distinctions. The benefits of the patented X-BOW® shape have been well documented, and include among other things, increased operating time, lower fuel consumption, smoother bow immergence, reduced operational disturbance and involuntary speed reduction, reduced emissions, better comfort and safer working operations. Enhanced ride quality and handling in rough seas makes this hull form ideal for the working vessels that the design has so far spawned. Many crews who work on XBOW ® ships do not wish to be assigned back to standard hull form tonnage due to the innovative bow form’s performance in rough seas. It is not unusual in this day and age for a newbuild to be fabricated at one shipyard and then fitted out and completed at the primary contract yard. Ulstein frequently employs this method and the hull of the Island Performer was built by the Crist Shipyard in Gdynia, Poland before being towed to Norway. Crist began operations in 1990 and has gone from strength to strength. The company concentrates on steel constructions and ship-repairs and has seized upon the growing markets in wind farms and offshore industries.
The yard belongs to a group of companies that serves customers in Poland, Germany, Norway, Denmark, Finland, Iceland, France, Belgium, The Netherlands and Scotland. Complete build projects are also undertaken and product variants include vessels and barges for the installation of wind turbines, platform supply vessels (PSV), anchor handling tug supply vessels (AHTS), offshore construction vessels, fishing vessels, tugs, ferries, container vessels and research vessels.
Well Equipped
The Island Performer is from the Ulstein SX121 stable and her configuration is for the petroleum industry. Upon delivery to ship owner Island Offshore the flexible, state-of-the-art RLWI/IMR vessel was placed on a five year contract with FTO (a joint venture between FMC Technologies, Edison Chouest Offshore and Island Offshore) in the Gulf of Mexico commencing in late 2014. The vessel is customised to suit the scope of work in the FTO contract, in which RLWI (Riserless Light Well Intervention) and IMR (Inspection/Maintenance/Repair) are the main tasks. She is able to perform operations at depths down to 3,000 metres and the very first assignment will be for the RogFast connection in Norway, in which the scope of work will be to investigate the sea bed.
Owner Island Offshore was founded in 2004 and is a leading provider of high quality solutions for the offshore oil industry based on a fleet of advanced high quality service and subsea service vessels. They currently have 13 Platform Supply Vessels, four Riserless Light Well Intervention ships, six Subsea Construction Vessels, two Anchor Handling Towing Ships and four Supply Vessels. A further five ships are on order. Island Offshore specializes in developing and implementing innovative engineered solutions for Light Well Intervention (LWI) to obtain increased oil recovery. Other subsea well operations using dynamically positioned vessels can also be performed to replace drilling rigs, and hence offer reduced costs for subsea operations. Worldwide there are more than 5,000 subsea wells. In order to increase oil recovery from these wells there is a demand for an efficient subsea light well intervention service. This includes repair, scale removal, installation and manipulation of mechanical devices (valves, plugs, screens etc.), perforations and re-perforations, zone isolation, fluid sampling, chemical treatment, well abandonment etc. Light Well Intervention technology reduces the intervention cost to roughly one third, enabling more intervention work and resulting in better exploitation of subsea wells. The long term objective is to increase the oil recovery on subsea wells from an average of 45% to 55%. Cost saving is the main impetus for performing LWI operations from a monohull vessel such as the Island Performer when compared to the same operations being performed from a drilling rig. These operations can be performed via dynamic positioning (DP2/DP3) enabled ships such as the Ulstein SX121 whilst maintaining well control and access to the well bore via a subsea lubricator system, resulting in a lower cost for intervention operations. The sizeable accommodation superstructure located forward on the Island Performer contains a hotel compliment with permanent capacity for 130 crew members. The accommodation is of high quality and fire retardant furniture in cabins. Floating floors on five decks provides low noise and vibration levels in the accommodation and as a result the ship offers the highest Comfort Class (COMF-V1). There are ten state cabins with separate bedrooms, three state cabins, 27 one-bed cabins, 45 two-bed cabins, a hospital and sick bay, a 70 seat mess room, three day rooms, smoking room, helicopter reception, auditorium, conference rooms and offices, a games & internet room, gym, galley, dry provisions room, two cooler rooms and two freezer rooms.
Other facilities include an ROV (Remotely Operated Vehicle) Workshop, Online room, Operation office, ROV offices, Laundry room and the mandatory Muster station. Atop the Bridge is the 26.10m diameter helipad with 20 corners and a safe working load of 12.80 tonnes. The ship’s lifeboats are nestled in cutaways on either side of the superstructure whilst a fast rescue boat is carried in a housing beneath the subsea crane. Aft of the superstructure is the Module Handling/Intervention Tower with a safe working load of 300t. The tower base measures 8.135m x 8.120m, the freeheight inside the structure is 31.325m and the net lifting height is 29m. The main AHC winch has an SWL of 140t and 2,500m of cable. The tower can be operated in active heave or constant tension modes. There are ten winches of three types installed, two sets of cursors plus an operator’s cabin. Subsea equipment is raised and lowered via this tower through an eight metre square moon pool (a vertical passage from working deck down through the vessel giving access to the water below) that has dampening chambers on all sides. The hatch cover over the moonpool has a hatch load of 250t. Operation is possible in sea depths of up to 3,000 metres using her DP mode to hold station over the work site. The Island Performer is DP3 enabled and for this role two operator stations are located on the bridge plus one emergency operator station.
The position reference systems used are Seatex DPS700, Mini RadaScan plus two USBL hydro acoustic reference systems. A second ROV moon pool, measuring 4.9 m x 5.0 m, with dampening chambers at all sides is also installed and is accessible to the starboard side mounted active heave compensated (AHC) electro-hydraulic pedestal crane with capacity to perform heavy lifting operations within demanding subsea and offshore environments. A safe working load (SWL) of 250t is achieved at a 14m outreach (Subsea) whilst the SWL is 83t at the maximum outreach of 36m (Subsea AHC). An auxiliary AHC winch has a SWL of 20t at a 40m outreach and has 500m of cable. One ROV carried can be craned over the ship’s side whilst the other is dedicated for use via the moonpool subsea access. Moonpool operation is also assisted by a shelter deck with a freeboard of 5.35m that stretches all the way past the main moon pool and aft to the main crane. This increases the operational window for moon pool work and offers a shielded space for various equipment. Arranged on the mid-ships 900m2 shelter cargo deck is a multi-skidding system for handling 100-tonne skidding pallets. The aft cargo deck area is 800 m2 with a freeboard of 2.40m and the deck load is 10 t/m2. Both cargo areas are served by the AHC crane. The anti heeling system consists of three heeling tank systems for crane operations complete with three reversible propeller pumps, each with a capacity of 800m3/h – 15 mWC.
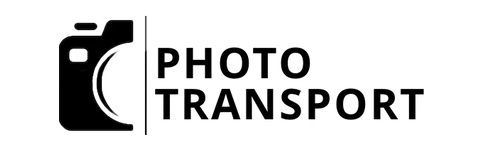
Performance at Sea
The Island Performer achieved a speed of 15.25 knots during sea trials and has a diesel electric propulsion system. Six Rolls-Royce C25:33 L9A main engines, each with an output of 2,880kW MCR/2,740ekW at 900rpm power three electric motors that are each controlled via a frequency converter to produce a performance range of 0-3000ekW and 0-1200rpm. At the business end are three stern mounted 3,000kW azimuth thrusters with nozzles and fixed pitch 3,200mm diameter propellers. Manoeuvrability is assisted by twin 2,140kW, 900rpm controllable pitch, variable speed and super silent running transverse bow tunnel thrusters. To assist with dynamic positioning when working at a set location at sea a retractable 2,000kW, 1,800rpm azimuthing bow thruster with a controllable pitch/variable speed propeller is installed. On board power is provided via six ABB type AMG06030LR08 LTA generators
The hull form, with the Ulstein XBOW ®, combined with diesel electric propulsion system, ensures good performances with regard to fuel consumption, sea keeping, station keeping, speed, and deck cargo capacities. The ship also features the “Operation+” philosophy that ensures even higher redundancy during operation. This allows the vessel to continue uninterrupted operations after sustaining a substantial single failure, such as the loss of generators or thrusters. This gives the vessel unrivalled extended redundancy, and the customer/operator a ship that they can fully rely on. An ESD (Emergency Shut Down) System is installed to minimize the consequences related to the escape of potential hydro carbons and H2S gases. The newbuild is an environmentally friendly ship in all respects. SCR (Selective Catalytic Reduction) catalysts are installed for all main engines and a Green Passport complying with IMO ship recycling recommendations has been issued. Prior to delivery the Island Performer was named on 27th June in Norway’s beautiful Geirangerfjord.
Ulstein X-Stern™
As this feature was being compiled in late August the Ulstein Group unveiled the X-Stern™, a design feature increasing operability through positive effects on station keeping, wave response, comfort and safety in harsh conditions. Developed following studies in the North Sea, an X-Stern™ vessel can stay on position in harsh weather with the stern towards waves, wind and current. For vessels where the best possible motion characteristics are vital, positioning the X-Stern™ towards the weather instead of the bow will be the Captain’s natural choice. This new concept leads to reduced pitch and wave drift forces, as well as eliminating slamming. Positive effects are reduced power and fuel consumption while on DP, or the possibility of operating in a wider sector with the same power consumption. The design also has several of the same characteristics as the X-Bow®, and additional ice operation capabilities. The gentle displacement reduces acceleration, pitch and heave, it improves comfort and safety, and the operational window is increased. There will be no sea on deck, and reduced ice build-up in cold climates, due to the stern shape and enclosed nature of the aft deck. Future subsea ships will surely feature this new stern – see the image above of how a vessel such as the Island Performer will look.
TECHNICAL SPECIFICATIONS
Contract Date: 19th December 2012
Keel Laid: 14th June 2013
Launched: 16th April 2014
Delivered: 8th July 2014
Yard No: 301
Shipyard (Hull) Czechosłowacka 3, 81-336 Gdynia
Shipyard: (Completion) Ulstein Verft AS
Places of Build: Ulsteinvik, Norway (Completion) & Gdynia
Type: 639 – Multi Purpose Offshore Vessel
Registered Owner: Island Offshore X KS, Care of Island Offshore Management AS, Staalhaugen 12, 6065 Ulsteinvik, Norway.
Registered Manager: Island Offshore Management AS
IMO: 9682045
Flag: Norway
Port of Registry: Alesund
Classification: 1A1 SPS SF COMF-V(1)C(3) HELDK-SH CRANE E0 DYNPOS-AUTRO NAUT-AW CLEAN DESIGN DK(+) BIS
Gross Tonnage: 12,983
Net Tonnage: 3,895
Deadweight: 8,600 (7,300 without tower mounted)
Length Overall: 130.00m
Length (waterline) 122.10m
Beam: 25.00m
Hull Depth: 10.00m
Scantling Draught: 7.615m
Design Draught: 7.00m
Propulsion Type: Diesel Electric
Machinery: 6 x Rolls-Royce C25:33 L9A, 2,880kW MCR/2,740ekW each at 900rpm
Propulsion Motors: 3x electric motors, frequency converter controlled each 0-3000ekW, 0-1200rpm
Propulsion: 3x main azimuth thrusters, nozzles, fixed pitch – each 3000kW with 3,200mm diameter propellers
Bow Thruster: 2x 2140kW, 900rpm controllable pitch Retractable Thruster: 1x bow azimuthing 2000kW, 1800rpm control lable pitch/variable speed
Trial Speed: 15.25 knots
Generators: 6 x ABB type AMG06030LR08 LTA
Emergency Generator: 450 ekW
Crew: 130 (Crew & Workers)
Tank Capacities: Fuel oil (MDO) 2,084m3/Fresh water 1,077m3/Ballast water 6,581m3 Module Handing
Tower Winches: 4x Guideline Winches SWL 5t; 4x Utility line winches, SWL 3t; 1x Cursor line winch, SWL 12t; 1x Man rider line winch, 0.15t
DP System: DNV AUTRO (IMO Class III / DP3)
Special thanks must go to the Ulstein Group’s Senior Public Relations Consultant Tonje Øyehaug Ruud for the supply of information and images. Photographs courtesy Ulstein Group/Tonje Alvestad/ Marius Beck Dahle. Unfortunately a GA Diagram or similar is not available owing to contractual constraints.
Comments
Sorry, comments are closed for this item