On 11th March 2014 DeepOcean UK, a subsidiary of DeepOcean group Holding BV, announced that the company had entered into a 7 year charter agreement with Maersk Supply Services, for a new build next generation cable lay vessel. The vessel was a DOC 8500, a Damen Offshore Carrier which had been designed specifically to suit DeepOcean’s requirements. The chartering of the DOC 8500 extends DeepOcean’s capabilities in the larger cable laying end of the market, representing a new focus on interconnector projects, in addition to oil & gas sector and renewables work. Owned and operated by Maersk Supply Service, the vessel will become the latest addition to the 60-plus strong Maersk offshore support vessel fleet.
The DeepOcean group was established in May 2011 following the merger of the survey, IMR (inspection, maintenance and repair) and decommissioning services of DeepOcean, the seabed intervention company CTC Marine Projects and the towing and supply services of Trico Supply. These three divisions provide the company with a set of complementary skills and expertise, which in turn, have positioned DeepOcean group as a leading provider of diver-less subsea construction services and operations. Now operating as one company under the name DeepOcean, it offers five main service streams including Survey and Seabed-mapping, Subsea installation, Seabed intervention, inspection, Maintenance and Repair (IMR), and decommissioning. CTC Marine Projects was established in 1993 as a private limited company in the North East of England. CTC’s initial core business was the provision of fibre optic cable lay and seabed intervention solutions for the global telecommunication market. Later, the company diversified and added trenching services for the oil and gas industry and offshore renewables. This sector is now the foundation of DeepOcean UK.
DeepOcean was itself established in 1999 and founded on the provision of high quality equipment and subsea services combined with a team of highly experienced personnel with knowledge of deep-water operations. DeepOcean now has the track record and experience to take on deep-water assignments anywhere in the world. Maersk Supply Service (MSS) entered the offshore market as the first Scandinavian shipping company in this sector in 1967. The company was established as an independent business unit in the A. P. Moller-Maersk group in 1974 and in 1979 the company became a leading owner and operator in the field of large offshore support vessels with the delivery of the first anchor handling tug supply vessel of more than 10,000 BHP. In 1998 MSS ordered the first of four dedicated cable vessels and ten years later MSS became Maersk Supply Service a/S, a separate limited company with its own dedicated HSEQ utility. The core functions of MSS are anchor handling in all water depths, moving offshore structures such as drilling rigs and barges, support for offshore crane vessels, subsea infrastructure assistance, transportation of equipment to and from rigs and production units plus the installation and pre-set of heavy mooring systems. This latest project for MSS builds on their long standing relationship with DeepOcean, supporting their subsea operations. The next generation DOC 8500 cable lay vessel, in combination with the Maersk Company’s survey and trenching capabilities, will enable MSS to bundle its services for customers in the offshore power cable and umbilical markets. The versatile new vessel will be well suited for installation and burial projects using her 7,000 tonne carousel from land-fall to deepwater and also in remote geographical locations.
Offshore Connections
The first Damen Offshore (DOC) 8500 was built for Van Oord NV, a leading Dutch offshore company. The 9,675gt vessel, christened Nexus, was delivered in 2014. The DOC 8500 design is a semi-customised, modular project and, being compliant with the ship-to-ship rule, the vessel has been configured to accommodate 90 personnel, mostly in single occupancy cabins. The vessel also acts as a flexible platform for both transport and installation work offshore. The bow and slender hull (akin to the PSV 3300 CD of which the World diamond is one example) optimise sea keeping in rough seas and suppress slamming. The ship will run on either MGO or HFO and has dP2 capabilities in line with offshore market preferences. The high on-deck cable carrying capacity makes it particularly competitive as a cable layer, while the vessel has also been optimised for shallow water operations, coming complete with a seven-point mooring system and the ability to take the ground fully loaded.
The second member of the 8500 family, ordered for the Maersk offshore and DeepOcean joint operation, began life as Yard No. 553015 at Romania’s Damen Shipyards Galati (DSGA). This is the largest of Damen Shipyards group’s 32 shipyards, repair yards and related companies worldwide. While Damen’s international sales organisation takes care of product development, self-managed DSGA has developed into a highly efficient production shipyard with a significant output. Since joining the group in 1999, the yard’s shipbuilding expertise and closely-managed supply chain have been behind some of Damen’s most important deliveries to date, fully representing the group’s diverse product portfolio. At the busy yard on the banks of the Danube, Damen’s unique shipbuilding concept comes to life. The hull of the new vessel was launched into the river on 23rd July 2015. The ceremony was attended by senior representatives of Maersk Supply Service, DeepOcean UK and the Damen Shipyards group. The newbuild had the appropriate name Maersk Connector bestowed upon her.
The cable layer has an overall length of 138.35 metres, a moulded beam of 27.45 metres, hull depth of 9.60 metres and summer draught of 6.25 metres. The 12 knot Maersk Connector’s gross tonnage is 10,678gt with a deadweight of 9,600dwt. The vessel boasts 2,200 m² of unobstructed deck of 20t/m2 load capacity with ro-ro capability.
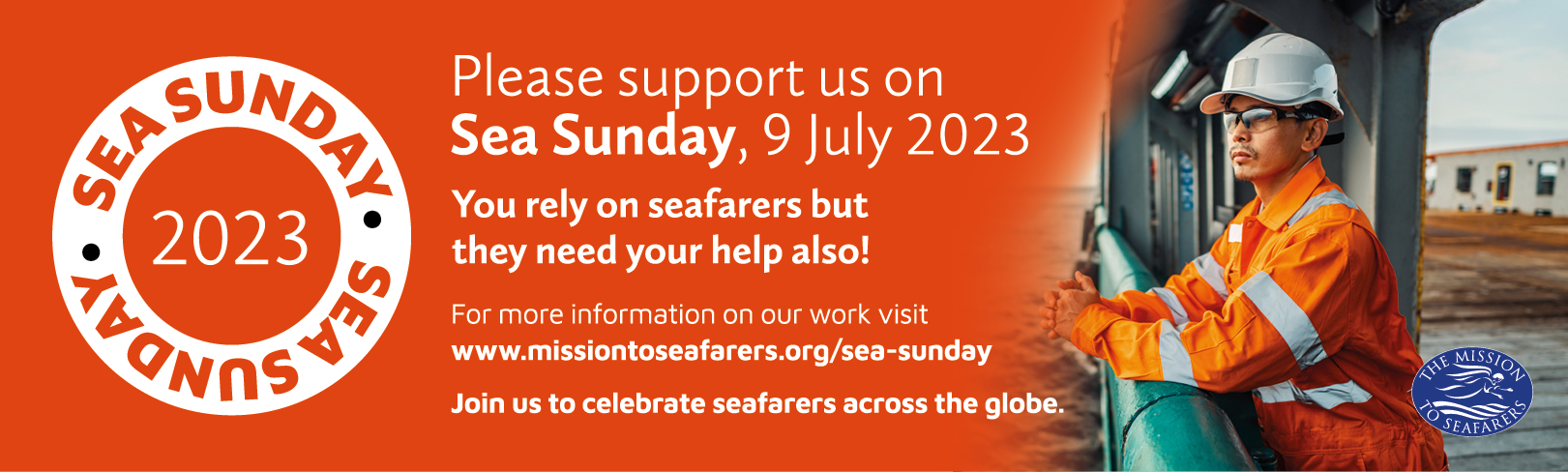
Located aft of the superstructure is the 7,000 tonne cable carousel with a second one able to be installed if required. The outer diameter of the carousel is 27m (adjustable to 29m) and the inner diameter is 5m (adjustable). The basket depth is 6m and this is also adjustable. Located aft of the carousel on the port side is an active heave compensated dP2 Northern Crane of the knuckle boom electro-hydraulic type. This subsea crane has a 50t safe working load at an outreach of 18m. Forward of the cable carousel is a rigid boom crane with a 10t safe working load at a 25m outreach. On the stern are the supports to fit a 60t capacity a-Frame for lifting equipment on and off the working deck. The aft area also houses the guides for feeding the cables from the carousel to the seabed including a 20t tensioner (a further two 15t tensioners can be installed). Other equipment on deck relates to the cable laying feed system plus the survey and trenching capabilities to meet the high standards demanded by North Sea oil and gas customers. The power cable trench plough (PCP) is of the self-loading subsea type and can backfill as it travels up to a depth of 3.30m whilst travelling along the seabed. Cable burial by ploughing has been clearly established as an effective and reliable method for burial of cables. Ploughs are simple tools that offer fast progress rates and work in a range of seabed types. Laying a submarine cable is a remarkably complex, hazardous and expensive business. Routes need to be surveyed, technology developed and the cable needs to be laid without being lost, broken or damaged. The seabed is as varied as any terrain on land so undersea cable expeditions have always started with surveys to find relatively flat and unbroken routes. The next problem is keeping the cable safe from accidental damage. The hazards down there include sharks, earthquakes and volcanic activity. Fishermen pose a far worse hazard than fish – deep-sea trawls routinely snag and break cables. These days, new cables tend to be buried using robot submarine ploughs that crawl along the seabed, hence the Maersk Connector employing a PCP.
The cable types laid are HVAC and HVDC power cable with a maximum diameter of 230mm. a 125hp remotely operated vehicle (ROV) is also present to assist and monitor cable laying duties, capable of submerging to a depth of 2000m. On the outside of the hull either side of the carousel is a hinged work platform that folds against the vessel when not in use. These are deployed when the carousel is extended to a 29m diameter. A removable bulwark can also be installed on the ship’s side in the area occupied by the ROV gantry on the port side, forward of the carousel. Contributing to production efficiency, the vessel is capable of grounding out with her seven point mooring system. This eliminates the need for a separate shallow water cable lay vessel and minimises the number of cable joints required. The bespoke carousel system accommodates bundled installation of high specification cables with no requirement to coil them.
The mooring system involves four winches with a 600kN pull/900kN hold, two winches with a 600kN pull/2,210kN hold plus six 7t dolphin anchors and one pull ahead winch with a 1,000kN pull/1,850 KN hold. The lower level of the superstructure, on the main (a) deck, houses freeze, cold and dry stores, coffee shop, galley, mess room, fitness room and assorted locker rooms. Above on B deck is cabin accommodation plus a conference room and offices. Officer and crew cabins can also be found on C and d decks. E deck consists of a helicopter reception room for 20 persons, officer accommodation and day rooms, office and emergency generator room. One level above is the Bridge deck and atop this is a heli-pad suitable for landing a Sikorsky S-92 helicopter.
Two decks beneath the working main deck is the Tanktop containing the propulsion room aft and engine room (forward) along with other areas including the three transverse tunnel thrusters. The main engines are two 2560kW MAK 8M25C engines. The auxiliary engines are two 1912kW MAK 6M25C units plus one 1400kW Caterpillar 3512C engine. The exhaust stacks are located aft of the accommodation, one either side. Propulsion is provided by twin azimuth Thrusters and manoeuvrability is aided by three 1250kW bow thrusters plus one retractable 800kW stern skeg. The six thrusters work together when dynamic positioning (dP2) mode is engaged during subsea operations. The Tweendeck above houses the upper area of the machinery room, engine control room, workshop and separator room (all forward), ballast water treatment rooms (midships) plus a cargo hold towards the stern, accessible from the working deck via two flush hatchways. The hold measures 12m long, 12m wide and 2.60m deep.
Put to Work
Following fitting out and sea trials the Maersk Connector was delivered on 4th February. The dP2 cable installation vessel was handed over from Damen Shipyards group to Maersk Supply Service. She went directly on a long-term charter for subsea services provider DeepOcean having been contracted to undertake marine works for three DeepOcean contracts: the Walney Extension Project, the Nemo link® interconnector and the Bligh Bank Phase ii offshore Wind Farm. In combination with new survey, trenching and installation equipment, much of which has been awarded to UK manufacturers, Maersk Connector enables DeepOcean to deliver more efficient, cost-effective and safer cable installation and will contribute towards maintaining the UK’s energy security and lowering the wholesale cost of electricity. The Maersk Connector’s first port of call was Newcastle, to be prepared for her debut contract by DeepOcean UK and was noted there on 8th April.
Special thanks must go to Ben Littler of the Damen Group for all the invaluable assistance with information and images.
TECHNICAL SPECIFICATIONS
Launched | 23rd July 2015 |
Delivery | 4th February 2016 |
Shipyard | Damen Galati Shipyard |
Yard No | 553015 |
Owner/Operator | Maersk Supply Service AS |
IMO | 9743813 |
Flag | Denmark |
Port of Registry | Hirtshals |
Classification | 100 a1, offshore Supply Ship, Helicopter landing area LMC, UMS D.P (A.A.), I.W.S., W.D.L. ECO (A, G.W., I.H.M., O.W., P) descriptive note- loading / unloading aground |
Ship Type | Cable layer |
Length Overall | 138.35 metres |
Length BP | 120.00 metres |
Beam (Moulded) | 27.45 metres |
Hull Depth | 9.60 metres |
Draught (Summer) | 6.25 metres |
Draught (Min) | 3.60 metres |
Gross Tonnage | 10,678 |
Deadweight | 9,600 |
Main Engines | 2 x MAK 8M25C @ 2560kW each |
Auxiliary Engines | 2 x MAK 6M25C @ 1912kW each & 1 x Caterpillar 3512C 1400kW each |
Emergency Generator | 1x 254 KVA – 203 KWE @ 60 H |
Propulsion | 2 x azimuth Thrusters 2100kW each |
Bow Thrusters | 3 x Tunnel Thrusters, 1250kW each |
Stern Thruster | 1x Thruster in Stern Skeg @ 800KW |
Service Speed | 11.70 knots @ 4,200kW |
Maximum Speed | 12 knots |
Economical Speed | 10 knots |
Dynamic Positioning | DP Class dP2 according DNV Northern North Sea Region |
DP System | MT DP System |
Fuel | MFO/HPO |
Crew Accommodation | 90 Persons |
Working Deck Length | 94 metres |
Working Deck Area | 2,580m2 |
Rescue Equipment | 2x lifeboats (each 90 persons) & 1x fast rescue craft |
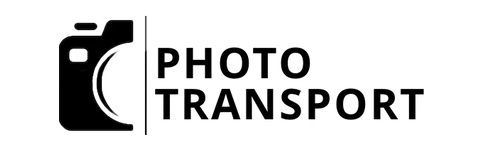
Comments
Sorry, comments are closed for this item