To enable ships of all sizes to navigate channels, ports, harbours and rivers their operators rely on dredging companies to maintain the navigable depths. Dredging is vital for economic growth and needs to be undertaken in all seasons and weather conditions. There are all manner of dredging options from the humble excavator seated on a barge to the state of the art self propelled and floating platform based trailing suction/cutter suction dredgers. The Netherlands offers a wealth of companies that design, build and operate dredging vessels and it is perhaps no surprise that the prolific Damen group is among the leading designers and builders. readers may recall that various products of the Damen group have featured in these Newbuild of the Month articles but the subject of this one began life on the other side of the globe. The Damen group boasts a range of Trailing Suction Hopper Dredgers (TSHDs), namely the TSHD 500/750/1000/1500/2000 and THSD 2500 ranging from 49m to 80.35m in length, 760t-3755t deadweight and 500-2500 cubic metres of capacity in the hopper for dredged material. The wide standard range of TSHDs have been designed as dedicated maintenance dredgers built around a modular concept, which means they are prepared for a large number of options. The basic version TSHD is a budget-friendly vessel perfect for efficient harbour and navigation channel maintenance. With the possibility of fully customising the dredgers, the standard TSHDs are highly efficient and fitted out to the latest technology standards. Durability has been a key consideration in the design process. a highly flexible concept of optional packages means that adapting the standard TSHD can be carried out effortlessly thus enhancing flexibility for the owner/operator. options can be added whilst in build or, should a specific dredging requirement be identified, later on when a vessel is already in service. The optional packages include self-discharging systems, bow coupling units, and degassing systems.
Double First
The inception of the first representative of the largest Damen Trailing Suction Hopper Dredgers, the TSHD 2500, took place in indonesia when ordered by the nation’s dredging company Pelayaran Fortuna Nusantara Megajaya (PFNM), based in Banjarmasin. This contract was also the first time that such a vessel had been built in indonesia. The order was placed with PT SteadFast Marine Shipyard in 2012, a unique project thus far for the facility that is located in Pontianak, West Kalimantan, indonesia. The keel was laid on 12th July 2012. The yard has the capacity to construct up to 15 ships per annum with 300 employees engaged in the construction of this TSHD over an 18 month period. The challenging newbuild was to become the Barito Equator, a name that was bestowed upon the ship on 3rd october 2014 during a launching and naming ceremony. So, why name her Barito Equator? The vessel will serve on the Barito river in South Kalimantan on the island of Borneo, indonesia whilst the shipyard is located in the City of Equator. This yard has also helped advance indonesia’s maritime ambitions through the transfer of technology during the complex build with Damen Shipyards group. The build took place with assistance from Damen Technical Co-operation (DTC), engineering from Damen Shipyards gorinchem and the complete trailing dredging system from Damen Dredging Equipment. Damen Marine Components delivered the rudder installation and gearbox as well as a host of other components. The PT Steadfast Marine yard has undertaken work for the Damen group since 2008. The Barito Equator was delivered to Damen Shipbuilding on 11th april 2015 and on 4th May she was delivered to Singapore for final inspection/handover by redwise, a global ship delivery and crewing company. Based in Spakenburg, The Netherlands redwise has specialised in the delivery of vessels on their own keel, under their own power since 1906. Ship delivery is a very specialised and unique profession in shipping with redwise having performed well over a thousand successful ship deliveries throughout the world. vessel types handled include bulk carriers, LNG carriers, trawlers, dredgers, tugs, workboats, crane barges, offshore vessels, ferries and many more.
Dredging the Depths
As mentioned above, the Barito Equator was built to maintain the economically vital cargo transport on the 890km long Barito river on the island of Borneo, indonesia. The country has invested large sums in capital projects to improve navigability on the waterway as the river is prone to heavy siltation which, combined with the extreme environmental conditions during dredging operations, demands highly reliable and efficient equipment.
The 2,554gt vessel has an overall length of 80.35m, a moulded beam of 16.20m, hull depth of 5.50m and loaded draught of 5.10m. The deadweight capacity for the dredged material hopper is 3,755t with the material discharged over a dumping ground via five rod actuated hopper doors located in the hull.
A bow coupling can also be fitted to permit discharge via a pipeline of up to 700m in length to a land reclamation project or similar. Bow discharge via the “rainbow” spraying method of pumping material directly out of a bow coupling (if fitted) is also available to a distance of 26m. The trailing suction system is installed along the starboard side of the hull and is lowered and raised on cables fed through two gantries that are themselves raised and lowered hydraulically. The suction pipe has a 750mm diameter and is powered by a diesel dredge pump. one fixed overflow is provided with a diesel powered jet water pump available for two of the three discharge methods offered by the TSHD 2500 design. The suction system can operate to a depth of 22 metres with the ship’s operational range being up to 8 miles from shore. The system can suck up sand, clay, sludge and even gravel from sea or river beds. a drag head is attached to the end of the suction pipe and lowered to just above the sea bed, making it possible to regulate the mixture of sand and water in its intake.
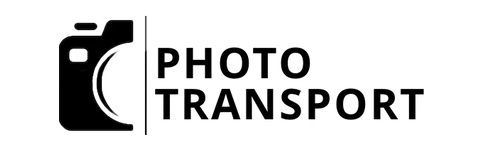
The Damen drag head is of a modern short and wide design to optimize flow and efficiency. The jetwater-assisted device follows the uneven sea bed profile and maximizes the mixture concentration.
The latest CFD software has been used to optimize the flow patterns of the transported sand and water mixture within the drag head. Cutting teeth and jetwater nozzles have been placed at an optimal position boosting the erosion of soil. Special attention has been paid to the robust and solid design of the welded steel construction of the drag head. This equipment can also be retrofitted to existing trailing pipe systems. The designers of the Damen dredging systems also identified the need to offer the standard trailing suction components separately due to normal wear & tear. These parts include all elements of the trailing pipe, as there are single and cardan hinges, the drag head, the turning gland and the slide flange. Moreover dredge valves can be supplied for efficient mixture control. For hopper fluidation purposes jet water monitors are also available. Such a monitor is installed on the ship with diameters for these varying from Ø150mm to Ø350mm, all designed for optimal hopper clearing. The steel nozzle has been designed to direct the flow exactly to the required location and is remote controlled in both the vertical as well as the horizontal direction and is designed for a maximum jet water pressure of 4.5 bar. a trailing suction hopper dredger generally stores the dredged material in its own hopper and discharges the left-over water overboard. a degassing system is also provided for port and harbour work. Cemented silt can be encountered in which gas bubbles are trapped and the amount of in situ gas can be extremely high resulting in the efficiency of the dredge pump being badly affected. However, efficiency can be boosted using this degassing system because it intercepts the gas before it reaches the dredge pump. Consequently harbour maintenance operations can be executed with maximum efficiency. The pump room is located on the Tanktop.
The Barito Equator is powered by a pair of CAT 3512C diesel engines, each with an output of 1118kW at 1800rpm. The propulsion is provided by two 2350mm diameter fixed pitch propellers housed in nozzles. Manoeuvrability is aided by a 746kW waterjet driven bow thrust unit but a 447kw fixed pitch propeller transverse tunnel thruster can be installed to the TSHD 2500 vessels. The speed at maximum draught is 11.20 knots. on board power is provided by two CaT C9 200ekW auxiliary engines plus a CAT C4.4, 46ekW emergency generator. The deck equipment includes two hydraulic anchor mooring winches with warping heads, one 5t working load capstan and one knuckle boom crane. The latter is located forward of the bridge on the starboard side, has a 10 tonne capacity at an outreach of 8.5m and is used predominantly for quayside to ship work such as supplies and equipment. in certain dredging conditions, a grab crane can be suitable but only the TSHD500, 750 and 1000 versions offer the ability to be fitted out with a specially designed grab crane, which is equipped with a wire-operated clamshell. The diesel-hydraulic driven crane is mounted on a pedestal integrated into the vessel, and all the crane systems are independent from the vessel’s systems.
The three deck superstructure (main deck/poop deck/bridge), located aft, houses the crew’s sleeping accommodation (officers single and Crew twin cabins), workshop, changing room, office, laundry, galley, cool store, mess room, day room and wheelhouse. at the time of writing the new vessel, resplendent in her orange and black livery, was in the Barito river estuary bound for Banjarmasin on the duties for which she was built.
Special thanks must go to Viktoria Adzhygyrei, Jan Hein Reeringh, Gerben Den Hartog & Gysbert Boersma of the Damen Group for their invaluable assistance with information & images.
Technical Specifications
Comments
Sorry, comments are closed for this item