Nexans S.A. is a global name in the cable and optical fibre industry and has its headquarters in Paris, France. The company can trace its immediate roots back to 2000 when Alcatel Cables and Components become Nexans but the corporate family tree stretches back to 1897 and the foundation of La Société Française des Câbles Électriques, Système Berthoud, Borel et Cie. The company was acquired in 1912 by Alcatel and became Compagnie générale des câbles de Lyon in 1917. Câbles de Lyon became Alcatel Câbles in 1986 and, 10 years later, Alcatel Câbles merged with Alcatel. Nexans is active in four main business areas, construction (local infrastructure, smart cities / grids, e-mobility), high voltage and projects (offshore wind farms, subsea interconnections, land-based high voltage), data and telecoms (telecom networks, data transmission, FTTx, LAN cabling, hyperscale data centre solutions), industry and solutions (renewable energies, petroleum, railways and rolling stock, aeronautical and automation). The Nexans Group is the world’s second largest manufacturer of cables after Prysmian S.p.A. Nexans Norway AS handles the supply of power, telecommunications, installations and heating cables in Norway, and is among the world’s leading manufacturers of offshore control cables and high-voltage submarine cables. The company develops, manufactures and markets submarine, land and offshore cables for power and telecommunication transmission. Wholly owned subsidiary Nexans Skagerrak AS is engaged in the transportation, laying and installation of submarine power cables and owns the 10,147gt/1976-built cable laying vessel Nexans Skagerrak. Nexans Norway is based in Oslo with operational sites in Rognan, Halden and Langhus.
Nexans Norway celebrated its centenary in 2015. The need to modernise, keep pace with Customer demands and meet the challenges of an ever-changing industry saw Nexans AS sign a shipbuilding agreement on 8th June 2018 with Ulstein Verft for a large, DP3, cable laying vessel (CLV) to support markets such as the offshore wind industry.
The world renowned and ground-breaking Ulstein Group is based in Ulsteinvik, the commercial and administrative centre of the municipality of Ulstein in Møre og Romsdal county in Norway. The town is located on the west side of the island of Hareidlandet, approximately 23km southwest of the city of Ålesund. Perhaps it is no coincidence that Nexans AS should select their compatriot Shipbuilder, Ulstein, to build their new ship but the vessel design and construction group has been in operation for 104 years having been founded by Martin Ulstein in 1917. Nowadays the company is run by his grandchildren, with Tore Ulstein as Chairman of the Board, Gunvor Ulstein as Deputy Chairman and Cathrine Kristiseter Marti as CEO. The Ulstein shipyard has sold over 50 X-BOW® ships since the company started to develop Ulstein designs in 1999. These ships are of different types including PSVs, anchor handling tug supply vessels, seismic vessels and construction and well stimulation vessels. They work in all weathers and have been a resounding success. Bourbon Offshore Norway believed in the new bow concept from the outset when the initial drawings were released and worked closely with Ulstein on the development of the first ship. The prototype was created as an AX104 series anchor handling tug supply vessel (AHTS) launched in 2005. Delivered in 2006, the 4,311gt newbuild was christened Bourbon Orca and subsequently received a number of awards, including the Norwegian Design Council’s design award, the Engineering Feat of the Year, and Offshore Support Journal’s and Skipsrevyen’s “Ship of the Year” Awards. Other vessels of the same design have since received similar distinctions. The benefits of the patented X-BOW® shape have been well documented, and include among other things, increased operating time, lower fuel consumption, smoother bow immergence, reduced operational disturbance and involuntary speed reduction, reduced emissions, better comfort and safer working operations. The Nexans AS order was a reminder that Ulstein still builds other hull forms. The ST-297 CLV, designed by Skipsteknisk, was one of the largest projects ever undertaken by the shipyard and it is not unusual in this day and age for a newbuild to be fabricated at one shipyard and then fitted out and completed at the primary contract yard. Ulstein Verft frequently employs this method and the hull of the Nexans CLV was built by the Crist Shipyard in Gdynia, Poland, before being towed to Norway. Crist began operations in 1990 and has gone from strength to strength. The company concentrates on steel constructions and ship-repairs and has seized upon the growing markets in wind farms and offshore industries. Complete build projects are also undertaken and product variants include vessels and barges for the installation of wind turbines, platform supply vessels (PSV), anchor handling tug supply vessels (AHTS), offshore construction vessels, fishing vessels, tugs, ferries, container vessels and research vessels. The Keel Laying ceremony took place on 24th April 2019, the grand blocks ceremony followed at CRIST, in the port of Gdynia, on 15th October 2019 and the completed hull arrived at Ulstein Verft under tow on 15th of June 2020. The hull, No. 314, was then towed into the dock hall to permit the next stages, including outfitting, electrical work, insulation and piping, to commence. Ulstein Verft also installed the main components such as the main generator sets, the power package, deck machinery, winches and topside equipment. The engines were installed in August 2021.
Northern Light Cabling
The name bestowed upon the 22,263gt, 156.40m long and 31.15m beam Cable Layer was Nexans Aurora, a name with a pleasing link to the multicoloured light displays of the Aurora Borealis that people flock to see in the skies above her home nation. The ship’s other vital statistics are a 17,331dwt, a net tonnage of 6,679t, a hull depth of 12.80m and a draught of 8.80m. The design of the Nexans Aurora is based on the combined experience of Nexans, Skipsteknisk, Ulstein Verft, and MAATS Tech. The aim was to produce a subsea cable and umbilical systems installation vessel for worldwide operations, covering the full range of shallow and deep subsea activities. The capability to install cables at even greater depths will contribute to securing the world’s energy supply and advancing the shift to environmentally friendly green electricity from renewables. Aft of the forward superstructure is the 10,000 tonnes capacity concentric split carousel/drum, the diameter of which fills the 31m beam of the ship. The carousel has a 450 tonnes under deck turntable tank beneath. The high-volume turntable reflects the high-capacity cable handling spread installed aboard the ship, which also includes dual product lay lines with capacities and features to handle safely and efficiently the full Nexans submarine systems product line of cabling, up to 400mm in diameter. Triple capacity bundling is also possible. The carousel is an innovative concentric design which allows either 2 cables to be processed in parallel, or a single long length cable weighing 10,000 tonnes. This minimises offshore jointing requirements which is a significant advantage technically and commercially. At the time of installation this was the largest offshore carousel globally. Nexans chose the ground-breaking carousel design as it best suited the deep water lay capabilities and enables the vessel to choose between a single cable load or dual lay capability with up to 5,000 tonnes in each basket.
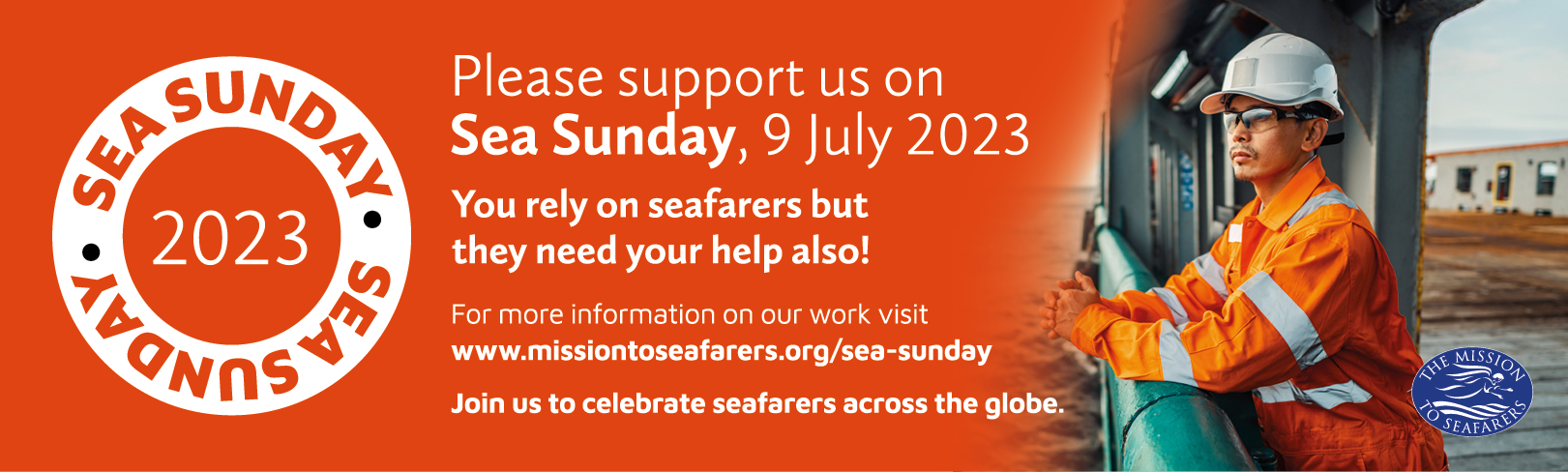
The port side laying line has Caterpillar tensioners for bundle lay (the cable passes between two sets of Caterpillar tracks as it is fed from the turntable through the ship and over the stern to the seabed) whilst the starboard side line has a smaller set of Caterpillar tensioners that work with a high-capacity cable capstan recessed into the starboard side of the working deck for deep water cable laying. The ship is prepared for vertical lay operations and complex subsea construction tasks in deep waters in addition to the principle built-in structural and system capacities and flexible design features to allow easy adaptation to a customer’s future needs. A dedicated enclosed cable splicing area is provided towards the stern, offering a controlled environment to perform all product splicing and termination work to the exact standard as performed in Nexan’s factories. Leading to the open stern work deck is a dedicated WROV hangar on the port side.
Nexans Norway and IKM Subsea signed an agreement for ROV services aboard the CLV Nexans Skagerrak, CLV Nexans Aurora and a third-party vessel for support services for a 3 year period plus 2 yearly options. MAATS has supplied the following equipment for this technology-rich vessel, 1x 10,000 tonnes Concentric Carousel, 2x Load Arms and Roller Pathways, 1x 75 tonnes Capstan System, 2x 25 tonnes Horizontal Lay Systems, 1x 5 tonnes Horizontal Lay Systems, 2x 3 t onnesHorizontal Lay Systems, 1x Bundling System, 2x Lay Wheels and 1x Control System. On 14th October 2020, the MAATS and Marine Fabricators installation team arrived at the Ulstein Verft shipyard to begin the installation of the paraphernalia, which began with the two lay wheels being fitted at the stern, which the cable is fed over before it goes subsurface. Following the lay wheels, final installation work was completed on the MAATS tensioners and 75 tonnes SWL Capstan. Palfinger Marine was chosen to deliver a major deck equipment package consisting of Abandon and Recovery (A&R) winches, A-Frame, knuckle boom cranes and overhead travelling gantry cranes. The array of equipment included 1x 150 tonnes A-Frame on the stern, 2x Active Heave Compensated Abandon and Recovery (A&R) Winches, 2x Auxiliary Abandon and Recovery (A&R) Winches, 2x Overhead Travelling Gantry Cranes, 2x Offshore Knuckle Boom Cranes and 1x Offshore Telescopic Boom Crane. Most of this apparatus can be seen out on the ship’s working decks. The stern working area is also overlooked by an observation and control room, giving the appearance of a rear-facing navigational bridge.
The robust profile of the Nexans Aurora reflects the fact that she was designed specifically to work in harsh environmental conditions and therefore required a boat deployment system with a high level of flexibility and redundancy. The ship’s delivery saw the operational debut for the first full-scale version of the so-called MissionEase system, developed by Norwegian davit supplier Vestdavit, that represents a significant design leap in launch-and-recovery systems for workboats and other craft carried onboard a vessel for a variety of tasks. Instead of a traditional davit mounted on the upper deck of a ship, MissionEase uses a system of hydraulic cradles to move boats on a tracking system within a hangar inside the hull to positions for maintenance, preparation or launch using a telescopic davit. The innovative system installed on the Nexans Aurora will have capacity to handle as many as 14 craft, including workboats and ROVs, that can be securely stored and mobilised in the enclosed hangar on the mission (working) deck. These will be used to carry out vital maintenance and other work on submarine cables for power supply and fibre-optical communication connected to offshore installations. Nexans, together with the shipyard, selected the MissionEase system due to its versatility as it enables multiple boats to be moved and safely launched from either side of the mothership even in rough weather. This avoids the risk of shifting weight loads when lowering and lifting boats in adverse weather conditions using a traditional gantry davit on the top deck where space was also limited on the Nexans Aurora due to the density of cable-spooling equipment onboard. Such a system gives the cable-laying vessel a wider operational window so she can continue working on time-critical offshore installation work, avoiding weather-related delays that can have a costly knock-on effect for the client in terms of tardy projects. MissionEase was proposed by the ship’s Designer, Skipsteknisk, during the conceptual phase of the new-build, given the system was one of very few suitable solutions available in the market that fitted with the vessel’s specifications. A particular challenge for using Vestdavit’s MissionEase was to make the system, including the telescopic davits, as compact as possible to fit within a confined space with height constraints on the mission deck, which is one deck below the aft hangar. Cutaways in the ship’s sides indicate the location of the vessel launching and recovery points. The DP3 capability Nexans Aurora is designed and equipped to be as self-contained as possible. This includes capacity for long range and long duration operations without re-supply as well as onboard facilities to ensure a high level of independence and reduced need for local support during operations in areas of minimal infrastructure. The superstructure design offers an inherent separation of the working and living areas, with the application of the highest work environment standards including exclusive use of single cabins for the 90 crewmembers and technicians. The accommodation areas are all located in the forward section of the ship with all the working equipment located aft.
Moving Forward
The Nexans Aurora is powered by six 3,450kW B33:45L6 Bergen Engines AS units that drive a trio of Azimuth AU115 3S Brunvoll AS Thrusters, each with a 3m diameter propeller. The Bergen B33:45L6 engine has a bore of 330mm and a stroke of 450mm, and runs at 450-750rpm as a marine propulsion engine or 720/750rpm for a 60/50Hz generator set drive. In line engines are the first to be produced, with 6, 7, 8 and 9 cylinders spanning a power range from 3,600kW to 5,400kW. The B33:45L6A engine is 9,280mm long, 4,100mm high, 2,180mm wide with a dry weight of 64,200kg.
Two Transverse Tunnel Thrusters of the FU 115 LTC3000 type are fitted in the hull at the bow (with 3m diameter propellers), and for Dynamic Positioning Class 3 mode (DP3) a single Azimuth retractable thruster of the AR115LNC2900 type is fitted (with a 2.9m diameter propeller). An Emergency Generator is installed in the form of a DI16M Scania CV AB unit. The ship’s service speed is 14 knots. Following sea trials, the final milestone of the Nexans Aurora’s construction was reached on 31st May when the DP3 Cable Lay Vessel, the state-of-the-art flagship of the Nexans fleet, was handed over from Ulstein Verft. The ship was delivered on time despite the parallel handling of the Covid-19 pandemic, with all the implications, restrictions and delays being dealt with in areas such as production, sourcing, travel restrictions, quarantines and much more. The vessel was then named in a ceremony at Ulstein Verft in Ulsteinvik on 8th June, before she departed for her home port of Halden where Nexans’ subsea high voltage cables competence centre is located. The ship’s lady sponsor was Mrs Anne Lise Aukner, former Managing Director of Nexans Norway. The Nexans Aurora’s first assignment is to install the export cables for the Seagreen offshore wind farm project. The construction on the 1,075 megawatt project started in 2021 and, when completed, the Seagreen 1 will be Scotland’s largest wind farm.
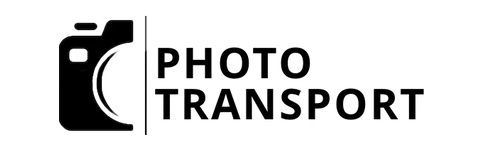
Comments
Sorry, comments are closed for this item