If you live almost anywhere in the Caribbean, chances are much of your food, supplies, and other commodities were shipped from the Port of Palm Beach, Florida, in the United States.
About 80% of the nearly 2.5 million short tons of cargo transitting the port annually is exported, with most of it shipped to countries in the Caribbean. The Bahamas gets more than half of its consumer products from the port. The port ships and receives nearly $15 billion worth of goods annually and is one of the area’s largest employers directly providing more than 2,700 jobs. An additional 6,000 jobs are associated with the importers and exporters that use the port to ship cargo.
Located on Florida’s southeastern coast, the port occupies 165 acres with the highest container volume per acre in the U.S. It was the fourth busiest container port in Florida in 2020, behind Port Miami, Port Everglades in Fort Lauderdale and Jax Port in Jacksonville. The port is also unique in Florida in that it is one of only two ports with on-dock rail.
More than a century old, the Port of Palm Beach opened on 18th January 1920, but it would take a few more years before its 4-foot-deep inlet was dredged deep and wide enough for cargo ships.
When the inlet was deepened to 18 feet, the port was visited by its first passenger ship, the 75-passenger Mary Weems, and its first cargo steamer, the Lake Chelan. Today, in addition to the port’s bustling cargo operations, the 1,680-passenger Margaritaville Paradise sails a two-night cruise from the Port of Palm Beach to Grand Bahama Island.
Railroad service played an important role in the development of the port, including a unique Havana Car Ferry service operated by the West India Fruit & Steamship Company that became the most prominent rail operation at the port. In its heyday, a fleet of five ferries offered carload freight service connecting the U.S. mainland and the Cuban capital.
Gateway to Cuba
Box cars were loaded aboard the seagoing ferries for an overnight trip to Havana, where the cars were rolled off the ship and turned over to the Cuban railways. On the return trip, box cars loaded with Cuban products were brought back to the port to be unloaded and sent on to their destinations via the Florida East Coast Railway (FEC).
For some 15 years, the car ferry remained the principal freight link between the U.S. and Cuba with the commerce between the two nations helping the Port of Palm Beach to become one of Florida’s leading ports. Rail traffic reached an all-time high in 1957 with more than half a million tons of freight being handled between the two countries.
Switching duties were handled by two oil-fired steam locomotives, originally built for the U.S. Army in 1942. In 1959, the port’s steam engines became the last of their kind in regular service anywhere in Florida, and among the very last steamers operating anywhere in the United States. Increasing maintenance and a lack of parts sent the steamers to the scrapper. Two replacement diesel locomotives were purchased that were older than the steam engines!
The days were numbered for the Havana service when the U.S. placed an embargo on most exports to Cuba in response to the increasing communist influence in the Castro government. In August 1961, the West India Fruit & Steamship Company ended rail service.
While the embargo devastated cargo traffic for years, the port’s railroad operations gradually regrew and, in recent years, have become even more vital. More than 14,000 rail cars move in and out of the port today, including intermodal cars, tank cars, gondolas and covered hoppers. Switching operations within the 6.5 miles of sidings in the port is enough to keep a single diesel engine and crew busy five days or more a week. The brightly colored GP-38-2 diesel switcher with a tropical motif now carries on the tradition of more than 35 years of railroading at the port.
In 1965, Perry Submarine Builders, owned by the publisher of 26 Florida and Bahamian newspapers, relocated to the Port of Palm Beach. The company designed and built small one and two-man submarines ranging in depth capability from 150 ft of sea water (FSW) to 600 FSW. Later changing its name to Perry Oceanographics, the firm expanded its operations, designing and developing numerous submersibles, saturation diving systems, remote controlled unmanned vehicles for global commercial markets as well as military programs for the U.S. Government. The firm also built the Lotus underwater car for the James Bond Film “The Spy who Loved Me”
President’s Wartime Bunker
Peanut Island, an 80-acre man-made island created when crews first dredged the Palm Beach Inlet, is owned by the port and contains President John F. Kennedy’s Cold War-era bunker. The bunker was built in 1961 for use if a nuclear attack threatened the President while visiting his Winter White House in Palm Beach. The bunker was refurbished in later years to become a unique tourist attraction.
Former President Donald Trump’s Winter White House and current residence at Mar-a-Lago also is located on Palm Beach a few miles south of the port.
Most of Peanut Island today serves as a beachfront recreation area and an environmental preserve accessible only by boat. It’s also a great viewing area for the many ships transitting the port.
Global Reach, Caribbean Lifeline
With more than 30 onsite tenants and users, the Port of Palm Beach today is an important distribution center for commodities being shipped all over the world, and especially the Caribbean Basin.
The port has three slips, 17 berths, and four roll on/roll off ramps for 6,500 linear feet of berthing space to accommodate vessels up to 700 feet long and 100 feet wide. The port’s berthing is 20 minutes from the first sea buoy to anchorage, with operating drafts of minus 33 feet mean low water (MLW).
The Army Corps of Engineers dredges the Palm Beach inlet on average every two years to manage the navigability. The sand scooped from the depths is used to replenish the beaches of Palm Beach.
Operations include containerized, dry bulk, liquid bulk, break bulk, roll on/roll off and heavy-lift/project cargoes.
The full-service, diversified port provides economic development within three surrounding counties through its designation as Foreign Trade Zone (FTZ) #135. The FTZ has offered companies millions of dollars in savings through duty relief or duty deferment since 1987.
The Port of Palm Beach cargo market is comprised of liquid and dry bulks, break bulk and containerized commodities transported between domestic and international markets. Grocery products, food products, beverages, and building materials are the key export commodities, accounting for 45% of the Palm Beach export market.
All of the exported raw sugar grown in south central Florida ships through the port, equating to more than 705,000 short tons annually.
About 130,500 short tons of molasses, a sugar by-product, are exported each year. More than 121,000 short tonnes of liquid asphalt, most of which comes from U.S. refineries, was shipped into the port last year to be used for road construction projects.
In response to a post-pandemic construction boom, bulk cement shipments by CEMEX, the largest supplier of building materials in Florida, have returned with the recent reactivation and expansion of the company’s 111,000 square-foot port terminal. The site had been inactive for 13 years and is expected to provide a healthy increase in vessel calls and cargo tonnage. The bulk cement is stored in large silos at the site. CEMEX’s U.S. network includes 10 cement plants, more than 50 distribution terminals, and 270 ready-mix concrete plants.
With its fleet of 17 vessels, Tropical Shipping has taken up where the West India Fruit & Steamship Company left off, providing cargo transportation services to 32 ports in the Bahamas and the Caribbean. Their services include refrigerated, Less Than Container Load (LCL), consolidation, cargo transfer, inland transportation, global partner and project cargo services. The firm owns and operates a wide range of equipment at the port including chassis, Gottwald mobile harbour cranes, Kalmar Gloria reach stackers, Kalmar diesel-electric straddle carriers, and jockey trucks to handle container lifting and shuttling.
Dry containers, insulated refrigerator containers and tanks are all handled. Piggyback and double-stack well cars are accommodated in the container rail yard. Containers arriving by truck enter at terminal gates, inspected, and moved to the marshaling area for loading onboard ships.
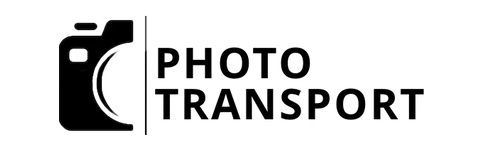
Specialized and heavy lifts have included electric transformers and other power industry equipment, a seaplane, building and construction equipment, heavy machinery, and iron and steel products.
Major facilities for world-class yacht service providers and builders, such as Rybovich Super Yachts and Viking Yachts, are located adjacent to the port. These facilities feature slips for in-water work, as well as land storage to handle larger projects and outfitting.
Port Statistics are:-
- Highest container volume per acre in the U.S.
- 2,492,709 Short tons cargo transitting annually
- 14.9 billion $ in goods shipped and received annually
- 80 Percentage of goods exported annually
- 1,392 Cargo vessels handled annually
- 266,431 Container units (TEUs) handled annually
- 14,288 Rail cars handled per year
- 6,609 Feet of berthing
- 7 Roll on/roll off ramps
- 2,700+ direct jobs
Cruise Ship Operations
Cruise ship operations were recently restored following the pandemic with the 52,926 gt Margaritaville at Sea Paradise, sailing twice a week from the Port of Palm Beach to Grand Bahama Island following a multi-million-dollar renovation. Formerly known as the Grand Classica, the ship operates as a partnership with Bahamas Paradise Cruise Line and entertainer Jimmy Buffett’s Margaritaville.
The Paradise has 10 passenger decks and 658 cabins in various categories. The main attraction is the ship’s Margaritaville signature design inspired by Buffett’s 1977 hit song. A Cruise and Stay program allows passengers to take an optional two-night stay at one of two resorts on Grand Bahama Island.
Paradise was built in 1991 as Costa Classica for Costa Cruise Line, then sold in 2018 to Bahamas Paradise Cruise Line to set sail as Grand Classica.
In addition to the Bahamas, the company could possibly expand its operations to other Margaritaville destinations in cruise ports in Jamaica, Cozumel, Grand Cayman, and Grand Turk, making a tour of Margaritaville’s around the Caribbean.
Cruise operations at the Port of Palm Beach are supported by a 40,000 square-foot two-story facility with baggage and U.S. Customs and Border Protection Agency facilities on the ground floor, and check-in and VIP areas on the second floor. A radial-telescoping, enclosed, adjustable-height passenger bridge is provided from the second floor to the cruise berth. The cruise ship currently is the only one to operate out of Port of Palm Beach.
Options for expanding cruise business include adding a second multiday cruise ship, a day cruise vessel, ferries to the Bahamas or Cuba, and attracting Itinerant luxury cruise ships.
Hurricane Disaster Preparation and Recovery
The Port of Palm Beach plays a vital role in disaster preparedness and business recovery in the Caribbean, Bahamas and Florida. Port staff collaborates with emergency management agencies, service providers, industry partners, and tourism associations in public/private partnership. Disaster recovery assistance is provided to businesses, individuals and governments after a catastrophic event, focussing on quick and efficient movement of recovery supplies to impacted locations.
The most recent example of this occurred on 1st September 2019 when Hurricane Dorian slammed into the Bahamas as a massive Category 5 storm, causing catastrophic damage on Abaco and Grand Bahama Island.
It is regarded as the worst natural disaster in the Bahamas’ recorded history and one of the most powerful hurricanes recorded in the Atlantic Ocean with winds peaking at 185 mph (295 km/h).
Most structures were flattened or swept to sea, with a death toll of 74 although many of those missing were unable to be found and accounted for. In addition to the loss of lives, some 30,000 people were left homeless and/or jobless.
Relief and medical supplies, food, water, temporary shelters, machinery, vehicles and teams of emergency personnel began flowing almost immediately from the Port of Palm Beach. Following that came millions of dollars in construction materials and supplies to assist in the years-long rebuilding effort.
Inland Port Offers Potential for Expanded Capacity
While opportunities are limited for purchasing or leasing properties around the Port of Palm Beach’s current 165 acres, an inland port currently under study for rural western Palm Beach County on the eastern side of Lake Okeechobee could expand operational capacity for the port several times over.
Studies and discussions have focussed on an anticipated 850-acre Inland Logistics Center (ILC) for materials distribution, warehousing, assembly and light manufacturing. The inland location would alleviate congestion along coastal highways by moving cargo onto rail lines and stimulate Palm Beach County’s economy by providing jobs and developing a huge tract of rural land.
While the ILC would primarily benefit the Port of Palm Beach, it could be expanded to serve all of South Florida. The project would be within 100 miles of three seaports, four international airports and three railroads with an abundance of undeveloped land, all assets that would help attract even more commerce.
A feasibility study concluded the region could benefit from the inland facility to warehouse goods and serve as a regional shipping hub, and the project has received approval for an economic feasibility study as the next step. Important questions still to be addressed include rail service expansion to accommodate inland cargo, environmental impacts, zoning, and project funding sources.
The port is governed by a five-member commission. The commissioners are actively involved in these studies and discussions. The commissioners are elected at large by voters within the Port of Palm Beach District, a political subdivision of the State of Florida. Although the port has the statutory authority to levy up to $200,000 annually of ad valorem taxes on all taxable property within the District to pay operating and maintenance expenses and the cost of capital improvements, the port has not levied any taxes since fiscal year 1974-1975.
Initially, much of the cargo traffic for the ILC could come by truck on highways already serving the area, but connections to rail lines would be needed. The Port of Palm Beach already has a leg up on this with its nearby connection between the Florida East Coast and CSX Railroads.
Once containers are discharged from ships and loaded onto rail cars, they would be transported from the on-dock facilities to the ILC. Designation as a U.S. Customs port of entry would allow cargo to be cleared there followed by further processing, transportation, storage, and/or distribution. Outbound containers for export would be brought to the ILC, loaded onto rail cars, and transported back to the Port of Palm Beach for loading onto outbound ships.
Advantages of the inland port include:
- Reduced congestion/faster transit, including improved access to major highways and other cities
- Reduced emissions with the use of rail transport
- Added space for importers/exporters to build warehouses and distribution centres at less cost than for facilities located in or near waterside ports
- Increased employment and economic development, with new investment from business and industry in surrounding area
Growing for the Future
The Port of Palm Beach continues to thrive with a significant redevelopment and upgrading of intermodal facilities and other improvements currently underway. These include an expansion program to double rail traffic capacity from 44,000 containers a year to 95,000, expected to eliminate about 29,000 truck trips on roads annually.
A forward-looking strategic Master Plan is focussing on expanding economic development, infrastructure development and improvement, intermodal transportation facilities and intergovernmental co-ordination. The plan will explore purchasing or leasing surrounding properties for expansion as well as what functions could be located or relocated there.
A nearby connection between the FEC and CSX Railroads could provide for the development of an inland intermodal logistics center on sites west of the port.
There may be future potential ferry service to the Bahamas and Cuba. If Port history repeats itself and Cuba reopens to U.S. markets, the first support items would likely be building materials, food stuffs, medical supplies, and other humanitarian aid cargo. These could be mobilized on container ships and brought to ports that can support small, short-haul freighters.
The nearby Palm Beach International Airport along with expanded hotel capacity in the revitalized downtown area provide a combination of convenience, service, cache, reputation, and operations/logistical ease for expanded cruise line operations.
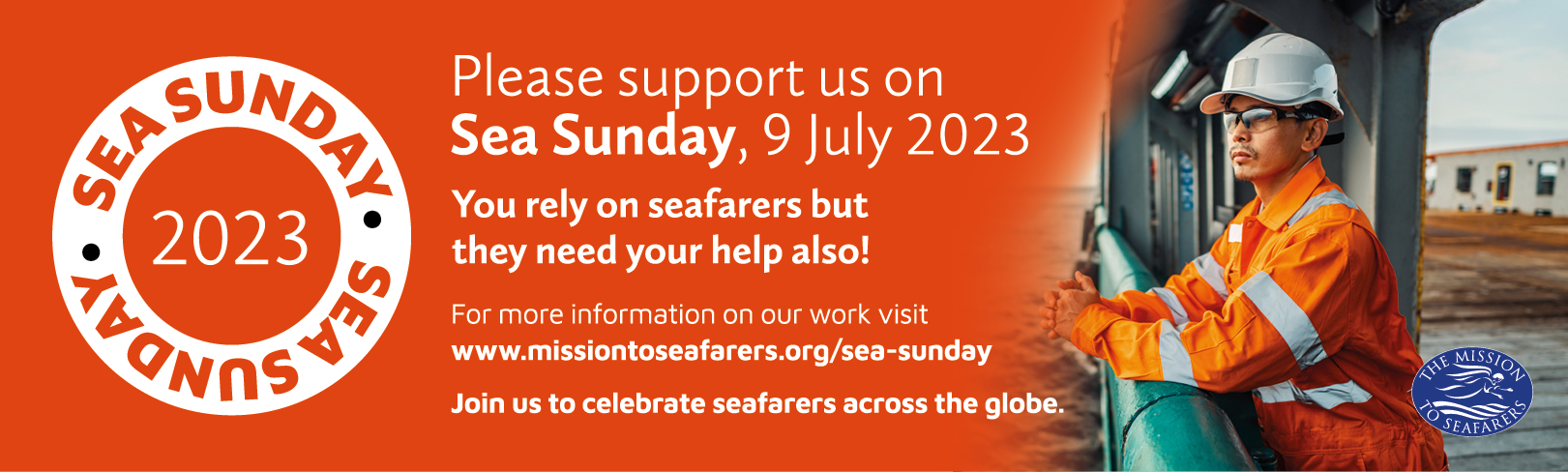
Indeed the future for the Port of Palm Beach is as bright as the tropical sun!
Comments
Sorry, comments are closed for this item