At the time of writing, KOTUG, a Dutch company based in Rotterdam and specialising in towage, has a fleet of 33 tugs. The roots of KOTUG (four generations of the Kooren family) date back to the initial activities of Antonie Kooren when he built his first tug in 1911. His son, Adriaan Kooren, registered the company Towage Company Adriaan Kooren BV in 1934 and started out as an independent towage broker prior to becoming a tug owner, whereby the tugs were employed in the dredging and port construction industry around Rotterdam. In 1977 Ton Kooren started Ton Kooren international Marine Services BV, mainly providing worldwide and deep sea towage. This sector of the company has since evolved into KOTUG offshore. In 1987 Ton Kooren also established KOTUG and started harbour towage. After Ton’s retirement in 2002, Ard-Jan Kooren was appointed CEO of KOTUG, a company that has expanded its innovative towage and related services to a worldwide level. The KOTUG brand name now encompasses all companies within the KMS group (Kooren Maritime Services).
Towage Evolution
KOTUG’s Ton Kooren was responsible for introducing the patented rotor Tug concept to the towage industry in 2000. This concept involves the use of three omnidirectional drive units of any type in a tug, in any triangular configuration. Essentially a rotor Tug is a true Tractor Tug with two Z-drives forward rather than Voith propellers, with the addition of a third drive unit aft. Conceived and initially used for working in the confined ports of Western Europe, especially in restricted canals and lock systems, a primary advantage of the triple drive system is that it can work very effectively in the sideways direction where space for conventional tug operations is constrained. This can involve simply pushing athwartships (working across the ship from side to side) with the tug, beam on to the ship’s side. The real merits of this tug format are in the operating configuration dubbed ‘rotoring’ in which the tug works at the ends of the ship and effectively within the beam limits of the ship. This operation means that the wash from the tug does not impact on the ship at all and is therefore far more efficient at controlling the vessel.
Canadian tug design specialist Robert Allan Ltd. concluded an exclusive agreement in 2012 with KST BV, (now rotor Tug BV, as opposed to KOTUG towage) to become the designer of all rotor Tugs worldwide. Like many maritime sectors, the towage industry has spawned “eco” variants in recent years including the rotor Tug family. The world’s first hybrid rotor Tug was the 463gt/2010 built RT Adriaan and, in March 2013, orders were placed for the first four of the new ART 80-32 rotor Tug design, the first project completed under the exclusive agreement between Robert Allan Ltd. and the KOTUG group. The Damen Shipyards group of the Netherlands was awarded the construction of two hybrid versions and Cheoy Lee Shipyards of Hong Kong was assigned to build two all-diesel propulsion variants (RT Discovery and RT Endeavour).
All four are equipped to a Fi-Fi 1 standard for firefighting. This feature focuses on the two hybrid ART 80-32 vessels that became the RT Evolution and RT Emotion. This class of rotor Tug offers a bollard pull of 80 tonnes and is 32m long, hence being known as the ART 80-32. Dubbed the E-KOTUG, a clever play on words, this environmentally friendly series offers a 50% reduction in harmful emissions, a significant noise reduction, cleaner combustion and substantial maintenance savings thanks to improved fuel economy. The optimised hull shape allows ahead and astern speeds in excess of 13 knots plus heightened stability, sea-keeping and escort performance. In terms of bollard pull, 84 tonnes over the stern and 82 tonnes over the bow is achieved. The advanced design concept benefits from enhanced operational characteristics including versatility, flexibility, and a rapid response to changes in manoeuvring requirements.
The E-KOTUG has a gross tonnage of 491gt, a displacement of 598t, a 12.60m beam, a 6.25m loaded draught and a hull depth of 4.82m. The Net Tonnage is 147t whilst the air draught is 16.50m. The hybrid capacity is generated by three Teco Westinghouse 500kW/60Hz electric motors, one on each shaft line between engine and propeller unit, complemented by two Corvus lithium polymer battery packs and managed by an intelligent XeroPoint Hybrid Propulsion System. This Aspin Kemp & Associates’ (AKA) system from Canada integrates electrical and mechanical energy to provide optimal operational modes, resulting in significant environmental and economic savings. The main engines are a trio of C rated IMO Tier II compliant Caterpillar 3512C TA/HD units with a power output of 5395 bkW (7095 bhp) at 1800rpm. These each drive a Z-drive Schottel azimuthing SRP 3000 FP fixed pitch propeller with a 2300mm diameter SDN55 nozzle. These units are arranged two forward and one aft and are located in individual compartments separated from the engine room by transverse bulkheads and watertight doors. Each unit is fitted with frequency controlled electric steering motors designed to achieve the required response time of one 360 degree rotation in 16 seconds. A twin disc MCD 3000-3 LD clutch controls each 1765kW propulsion unit.
Auxiliary machinery consists of one Caterpillar C18 TA (575 kVA, 50 Hz, 230/400v AC) and one Caterpillar C9 TA (250 kVA, 50 Hz, 230/400v AC). The Hybrid propulsion system is operated from a panel on the wheelhouse console. The controls offer Hybrid or Non-Hybrid propulsion plus the control modes of Stop, idle, Transit 1, Transit 2 or assist. With engines on stop in hybrid mode all systems are battery powered. When fully charged the batteries can maintain vessel services for up to 8 hours. Once the battery capacity falls below 30% one auxiliary generator will come on line. Alternatively if shore power is available the batteries can be charged and the vessel systems maintained. In idle mode thrusters are powered by the motor/generators in the shaft-line on batteries alone, enabling the tug to maintain position with a maximum speed of 3 knots for around 60 minutes. In Transit 1 mode the thrusters are powered by the motor/generators with both auxiliaries running to give speeds of up to 7 knots.
The vessel systems are also powered with any surplus power utilised to charge the batteries. When Transit 2 is selected the port and starboard thrusters are powered by their electric motor/generators from the main switchboard and the centre (aft) main engine drives the aft thruster to give a vessel speed of up to 11 knots. The motor/generator in the aft shaft line acts as a generator and if necessary one auxiliary will go on-line automatically. Finally, in assist mode all thrusters are driven by the main engines for towage assistance and speeds of up to 13.5 knots. The engines and generators power the on board services and any surplus power is again used for battery charging. The service speed is 12.50 knots, with a maximum speed of 13.50 knots possible. These vessels also offer a stepping capability to port and starboard at 7.5 knots whilst the forward and astern bollard pull is 80 tonnes, but this can be exceeded as mentioned above.
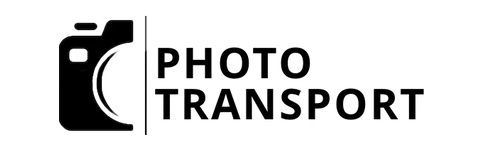
A towing winch is installed fore and aft on the main deck. The forward winch is a DMT, aTW-E22K2-300kN, single drum unit with a first layer capacity of 30 tonnes at 0- 15m/min/10 tonnes at 0-45m/min. There is 250m of 70mm diameter wire and 220m of 88mm diameter wire. The holding force is 225 tonnes. The stern winch is a DMT, SHW-E300KN, single drum unit with a first layer capacity of 30 tonnes at 0-15m/min /10 tonnes at 0-45m/min. There is 250m of 70mm diameter wire and 220m of 88mm diameter wire. The holding force for this winch is also 225 tonnes. Bunker capacities for the E-KOTUGs include 204.6m3 of fuel oil, 32.80m3 of fresh water, 2.40m3 of lubrication oil each for engines and Z-Drives plus 3.10m3 of hydraulic oil. Other equipment includes a JRC, JMA-5312-6 sea radar, a JRC, JMA-610-7 river radar and a JRC, JFE-380/25 echosounder.
The crew of six are accommodated in heated and air-conditioned living spaces, consisting of two single crew cabins and two double crew cabins, a galley/mess and sanitary facilities. There are two accommodation decks, lower forward (stores/2xs double crew cabins, switchboards/ hybrid room/laundry) and the main/forecastle deck (Master & Chief Engineer cabins/galley/mess/lounge). The 360 degree visibility wheelhouse is located one deck above this. Shiphandling fenders at the bow comprise an upper row of 800 mm diameter cylindrical rubber moulding with a lower course of ‘W’ section moulded rubber blocks. The stern is protected in the same manner and the sheer lines have two rows of ‘D’ section 300 mm x 300 mm lightweight Polymarine foam moulding.
Emotion-al Deliveries
The RT Evolution and RT Emotion (RT being an abbreviation for rotor Tug and the “E” names reflecting the E-KOTUG status) were completed by Damen Shipyards Hardinxveld which, as the name suggests, is a member of the Damen Shipyards group and specialises in custom built, medium sized vessels and general repairs/maintenance of inland/coastal vessels. The Hardinxveld yard, where Damen was founded in 1927, is one of the oldest yards of the group and therefore boasts 80 years of experience, knowledge and know-how on practically every technique and aspect required for newbuilding and repair jobs.
The yard is situated on the north bank of the river Merwede and has two separate slipways, one for steel and one for aluminium/polyester works with a total area of approximately 5,500 m². Both slipways are completely covered, condition controlled, protected from weather influences and equipped with indoor workshops and stores. The facility also has a number of outfitting pontoons (total length approximately 115 m), a carpentry factory, a piping department and a separate painting location. As is commonplace nowadays the construction of the tugs was sub-contracted to the Safe Co. Ltd. shipyard in Gdynia, Poland. This shipyard evolved from a Steel Production Plant in 2003 in the area of the Port of Gdynia known as Indyjskie Quay. In 2012 the shipyard also acquired a bigger site in Gdansk. The facilities produce a plethora of working vessels including shoalbusters, dredgers and various types of tug.
The latest KOTUG fleet members began life as build numbers 571714 and 571715 and were launched by Safe Co. Ltd. on 7th March and 2nd July 2014 respectively. The RT Evolution was launched from floating dock No.3 at the Navy Shipyard and the RT Evolution was launched from a floating dock at the Nauta Shipyard before being united, made ready for sea and towed in turn to The Netherlands for completion at the Hardinxveld yard. The keels for both tugs had been laid on 14th august 2013. With the RT Evolution having gone first, the RT Emotion left Gdynia under tow by tugs of the Dutch company Herman Senior BV in December 2014. After a stormy passage across the Baltic the ensemble arrived in Rotterdam on 27th December. The newbuild duo was then delivered by Damen Shipyards on 15th October 2014 and 30th March 2015 respectively.
The RT Evolution was christened on 18th May 2015 at the Greenwich Ship Pier on the river Thames in London during the cocktail reception of the ‘Tugnology Conference’. Mrs Elizabeth Brunton-reed, spouse of The ABR Company’s Chairman Mr Allan Brunton-reed, performed the naming ceremony in attendance of her family and Tugnology delegates. KOTUG chose the sponsor lady to express its appreciation and gratitude for the commitments and achievements of The ABR Company in relation to maritime industry orientated conferences, exhibitions and Tug & Salvage magazines over the past 25 years. The RT Evolution began her working career in the Port of Rotterdam on 1st December 2014. Prior to her naming, the RT Evolution worked on the river Thames including the maiden arrival of the new cruise ship Viking Star on 12th May 2015. At the time of writing there was no record of the RT Emotion’s naming ceremony but she sailed from Rotterdam on 16th April to Bremerhaven on one electric motor in full hybrid mode, to commence her operations for KOTUG’s European harbour towage division.
Special thanks must go to Jan Hein Reeringh (Communications Advisor), Viktoria Adzhygyrei and Karlijn Pott (P.R.-Tugs) of Damen Shipyards for their invaluable assistance with information and images.Technical Specifications
Contracted Builder | Damen Shipyard Hardinxveld |
Contracted Shipyard | Hardinxveld Giessendam, Netherlands |
Sub-Contracted Builder | Safe Co. Ltd. |
Sub-Contracted Shipyard | Gdynia, Poland |
Yard No. | 571714/571715 |
IMO | 9691357/9691369 |
Flag | Malta |
Port of registry | Valletta |
Ship Manager | Kotug international BV (Both Tugs) |
Ship owner | RT Evolution Ltd./RT Emotion Ltd./Elisabeth Ltd., Gzira, Malta |
Launched | 7th March & 2nd July 2014 |
Delivered | 15th October 2014/30th March 2015 |
Christened | 18th May (RT Evolution) & ?? (RT Emotion) |
Type | Harbour and coastal berthing tug, |
Class | Lloyds Register, 100a1 Tug, LMC, UMS, IWS |
Gross Tonnage | 491.00 |
Net Tonnage | 147 |
Deadweight | 350 |
Displacement | 598 |
Length overall | 31.95 metres |
Moulded Beam | 12.60 metres |
Draught (Loaded) | 6.25 metres |
Hull Depth | 4.82 metres |
Speed | 12.50 knots (13.50 knots Maximum) |
Bollard Pull | 80.00 tonnes |
Main Engines | 3x Caterpillar Type 3512C Ta/HD+ |
Power output | 5395 bkW (7095 bhp) @ 1800rpm |
Propulsion | 3x Schottel SRP 3000 FP fixed pitch propellers |
Propulsion Unit Diameter | 3x 2300 mm SDN55 nozzle |
Clutch Equipment | 3x Twin Disc MCD 3000-3 LD |
Propulsion Motors | 3x Teco Westinghouse 500kW, 60Hz |
Auxiliary Machinery | 1x Caterpillar C18 TA (1x 575 kVA, 50 Hz, 230/400v AC) & 1x Caterpillar C9 TA (1x 250 kVA, 50 Hz, 230/400v AC) |
Crew | 6 |
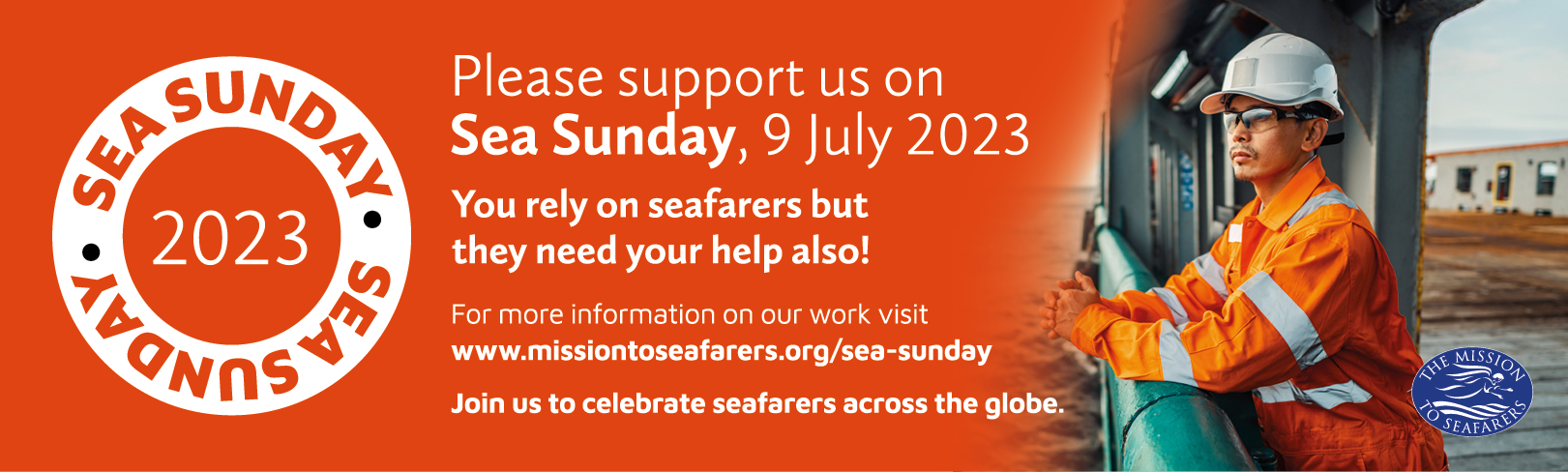
Comments
Sorry, comments are closed for this item