This month the “Newbuild” feature is a little different as the subject is the RNLI’s purpose built all-Weather Lifeboat Centre, a newbuild for newbuilds so to speak. The writer has had a life-long fascination with the RNLI thanks to his Father’s interest and his Uncle being an Engineer on the Yarmouth (I.O.Wight) lifeboat for almost 35 years. Childhood memories of polishing brass and copper aboard Yarmouth’s Arun Class lifeboat, RNLB Joy & John Wade, and ad-hoc visits to lifeboat stations and repair yards around the country during family holidays are still like it was yesterday.
Consolidate & Prosper
The British royal National Lifeboat institution has saved 140,000 lives since its inception in 1824 with the 190th anniversary being celebrated in 2014. it began as the brainchild of Sir William Hillary, who witnessed the tragic loss of life from dozens of ships that foundered in the Irish Sea off the isle of Man. initially the organisation was known as the National institution for the Preservation of Life from Shipwreck. The name was changed to the now household name of royal National Lifeboat institution (RNLI) in 1854, and cork lifejackets were first issued to crew members in the same year. With the support of London MP Thomas Wilson and West India Merchants Chairman George Hibbert, the institution was founded as a charity on 4th March 1824. Today, the RNLI has an active fleet of over 340 lifeboats, ranging from 3.8m to 17m in length, as well as a relief fleet. There are also four active and three relief hovercraft. The RNLI’s 4,600 volunteer crew men and women are on alert 24 hours a day, all year round to launch from one of the charity’s 236 lifeboat stations around the coasts of the UK and Republic of Ireland.
As well as lifeboats the charity now operates lifeguard units on over 180 beaches, has a specially trained flood rescue team and runs an international programme helping to set up and train lifesaving organisations around the world. The RNLI has been based at Poole in Dorset since 1974 and the site includes the administrative headquarters, lifeboat support depot (1976) plus college and support centre (2004). Historically new lifeboats have been constructed at key boatyards around the UK and serviced by those and other yards. Being a charity, the RNLI has to account for every penny of expenditure, and multiple building and servicing sites, not to mention the tender process for work contracts, does not necessarily promote efficiency.
A programme of self sufficiency produced the inshore Lifeboat Centre (ILC) at East Cowes, Isle of Wight, which evolved from its inception in 1963 into a site that could construct up to 60% of the lifeboats required by the RNLI in its own purpose-built manufacturing facility, with 1,685 craft built to date. Fifty lifeboats are now constructed at the centre each year, while up to 200 are serviced and refurbished there. The facility is highly respected across the globe as a centre of excellence for the building and maintenance of inflatable and rigid inflatable lifeboats, including the B Class and D Class lifeboats, the lifeguards’ inshore rescue boat and the Arancia (which are constructed under licence from Arancia of New Zealand). Newbuilds for The Netherlands, Iceland and Poland are also handled. Gradually the site has grown and there is now a large building to house the production of the Atlantic 75 and Atlantic 85 rigid inflatable boats (RIBs), which incorporates a dedicated laminating shop, spray booth, machine shop and welding bay employing a team of over 70 boat builders, fitters, electricians and solutionists including apprentices as well as supporting office and stores persons.
The FBM yard in West Cowes produced many all-Weather lifeboats for the RNLI (until its closure) including the Arun Class and present day 17 metre Severn Class. Other lifeboat building yards included Babcock at Devonport Dockyard and Berthon’s of Lymington, a yard reputed to have been in use since 1272 during roman times and has developed considerably over the following centuries as building techniques, fabrication materials and vessel types have evolved. Classes of lifeboat to be handled at this location include members of the Severn, Trent and Shannon series. Adjoining the yard is SAR Composites Ltd, an RNLI subsidiary that also took over the production building program from Southampton’s green Marine. The latter had built over 140 composite hulls for the RNLI since 1988 through the Mersey, Trent, Severn, and Tamar classes (the names representing rivers around the U.K and Ireland). The SAR Composites facility opened in April 2009 on a former green Marine site using their expertise and a team of 30 personnel.
New Era for Newbuildings
On 10th January 2013 the RNLI received planning permission from the Borough of Poole allowing the charity to build a facility at its Poole HQ to bring all-weather lifeboat production in-house. The announcement concerning the new RNLI all-Weather Lifeboat Centre (ALC) secured the future of all-weather lifeboat production and maintenance in an era when long serving boatyards were falling by the wayside or being increasingly unable to meet requirements. The projected cost for the ALC was £11.2 million but, once up and running, would save the charity £3.7 million every year. Taking into account the timeline towards full production and maintenance, the centre is expected to pay for itself in less than 10 years. Donations received need to be optimised so the benefits of bringing the work in-house are literally priceless. The RNLI can be its own customer so will have a “guaranteed order book.” Planning for future lifeboat requirements means that six new all-weather lifeboats will be needed annually for the next 20 years. Savings elsewhere in the RNLI provided £6.2 million for the project with fundraising providing the remaining £5 million.
The keys for the new ALC were handed over in March 2015 with the major contractor having been J.B Leadbitter & Co. Ltd. (Bouyges UK Ltd.). The project took 2.5 years from the original submission of a planning application through to approval and finally construction of the building. Prior to the ALC being built, the site of the former Bolson’s Boatyard, a total of 17,833m2, was cleared of the existing Lifeboat Maintenance Centre to then permit a local strategic flood risk assessment that required both the site ground level and its surrounding quay wall to be raised before the facility was built by 1.4m and 1m respectively. With the quay wall this was achieved by rebuilding the wall using cap and beam construction on a new sheet piled wall. But arguably the more significant challenge involved raising the ground level across the entire site. The additional ground material required for this purpose comprised reused crushed aggregate from the former shipyard and 15,000m³ of sand imported onto the site. At one point this mountain of imported sand stood up to 4m high before being laid across the site. In order to ensure that the new sand achieved sufficient settlement on the ground, the subsurface peat layer had to be dried. This process, known as surcharging, essentially involved squeezing the water out of the ground via wicks inserted through the sand and into the peat layer below. Once this process was completed, the piling could begin.
Over 2,000 Vibro Concrete Columns (VCCs) were laid across the site. Vibrating piles of this kind are particularly suited for sites such as this that contain weak alluvial soils and peats where traditional high-impact methods of piling may aggravate more fragile ground conditions. The only area where this method deviated was along the quay wall where pre-auger piles were used. VCCs, a ground improvement technique, transfer loads to the sands which are approximately 4m to 7m below the original ground level. The piles were laid out in a 2m grid but a complex logistics plan was established that enabled the piles to be laid incrementally around the mounds of sand and crushed concrete intermittently dispersed across the site. Axle loads of up to 60 tonnes were specified for the ALC which is comparable to the loading accommodated in airports so the groundwork had to cater for this, using load-transferring foundations. The total number of paving blocks that have been laid around the building totals 385,000. The ALC building comprises a 3-span steel portal frame that houses two barrel-roof building volumes separated by a covered central courtyard. The buildings are clad in composite steel and aluminium, and covered by a Kalzip standing seam roof. Building a contains a three-storey boat hall with a clear span of 50m x 20m while Building B contains an even bigger boat hall with a clear span of 70m x 20m. Both halls are designed for the production of boats and can accommodate several boat hulls at any one time. The extraordinary additional structural capability this requires has ensured that the building’s steel sections alone weigh 12,000 tonnes. They also incorporate proprietary ties and connections as the steel is too thick and dense to be directly drilled into.
Official Opening
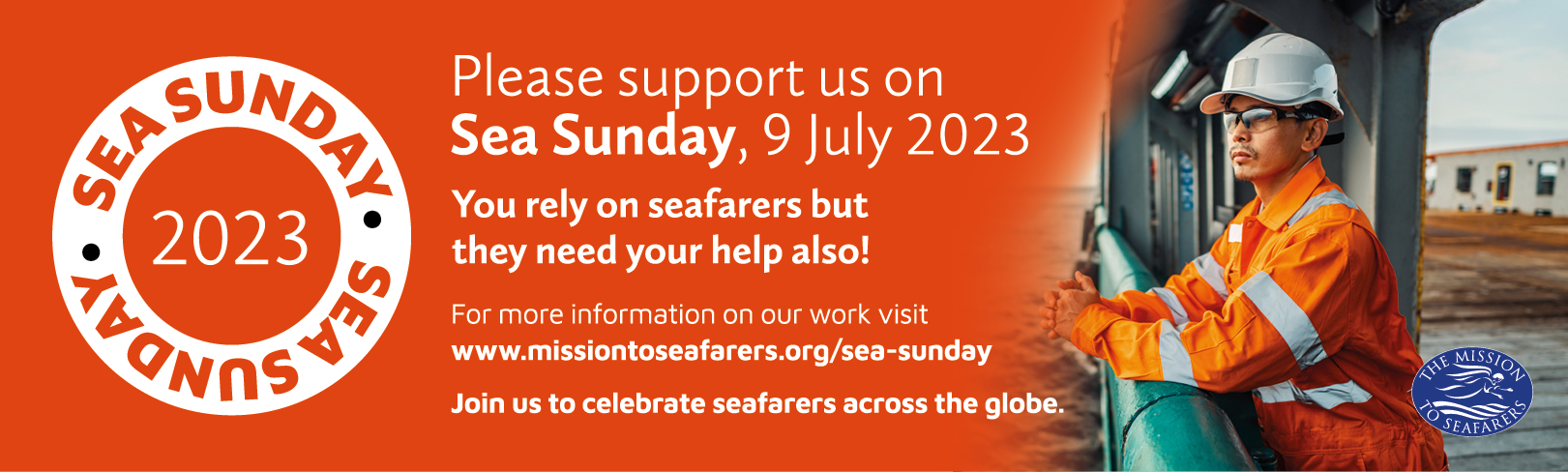
Friday 21st August saw the official opening of the new ALC, attended by around 500 guests.
RNLI Chief Executive Paul Boissier addressed the gathering (above) with two of the RNLI’s youngest fully qualified crew members, John McDermid (17) from Arranmore and Caryl Jones (20) from Porthdinllaen, ringing a bell as the doors of the ALC rose for the first official time. This bell will be rung every time a newly built ALB is launched. Phil Coulter’s Lifeboat anthem ‘Home from the Sea’ played to mark the occasion. The new facility was also opened to the public on 22nd/23rd August.
The ALC will become a British centre of engineering excellence and has revolutionised the lifeboat construction and maintenance programme, bringing every stage of the production process under one roof. This will ensure that the RNLI is fully equipped to build the new generation of 25 knot lifeboats. The lifeboat maintenance operation was moved to Cobbs Quay, across the water at Holes Bay, during the ALC construction but the 30 personnel moved back once the site was complete.
In addition, 19 people have been recruited in phases since September 2014 and from September 2015 six apprentices were also welcomed. around 225 people will eventually work within the new building, this figure comprising 150 production staff and approximately 75 in office space above Buildings a & B. Lymington based SAR Composites will transfer all operations to the ALC by 2019. From March 19 inshore training and Poole based relief lifeboats will be maintained and repaired in the ALC this year alone, including Atlantic Class 75 and 85 and D Class boats whilst 20 all-weather lifeboats will undergo refits and modifications, including relief fleet support, from right across the fleet.
Interim repairs will still be out sourced to existing RNLI partner boatyards when it is not viable to return a vessel to the ALC but, with the exception of the inshore lifeboats handled at the dedicated build facility at East Cowes, all lifeboats will now be built on the ALC site. The lifeboats have a 7 year overhaul cycle per vessel and the newest 25 knot designs have a 50 year life expectancy for the hull & superstructure. (Fabricated from composites). When viewed from the approach road, Building A is to the left and Building B is to the right, joined by the central covered courtyard. The latter can be used for quick all-weather maintenance tasks year-round whilst the lifeboat remains in the self propelled hoist and also offers shelter when lifeboats are moved between bays in both buildings. Building a measures 85m x 30m and has a workshop floor space of 5,000m2. This vast space is essential in order to enable several boats to be constructed, maintained and repaired all at the same time.
The lifeboat maintenance/build bays in each building measure 20m long by 10m wide. The roller doors across each bay and two of the paint preparation/completion bays measure 10m wide by 10m high. The bays are the size they are to cater for a Severn Class lifeboat, the RNLI’s largest, complete with aerials and fittings. The three bays in Building A are primarily for the construction of the lifeboat hulls with air purification and ventilation to cope with the tasks undertaken in this environment. A mezzanine level runs along the rear of the bays permitting direct access onto the lifeboats housed there and the storage of tools etc. close to where they are needed. When required, a raised walkway cell mirroring the hull profile is put in place around the vessel removing the need for ladders. In the ceiling of each building is a sliding welded gantry crane, capable of hoisting up to five tonnes for the manoeuvring of heavy components.
At the rear of Building A are the three paint shops, one smaller and two of the aforementioned 20m long/10m wide and 10m high size. The left-hand side booth and smaller right-hand booth are for the preparation processes with the central booth being of a sterile environment where the top coat paint layers are applied. Again, the two large bays can accommodate a Severn Class complete. The yard outside of Paint Shops 1/2/3 includes dedicated areas where vessels are cleaned once lifted from the water, with all run-off draining in to tanks below ground. At the opening event two “naked” Shannon Class composite hulls/superstructures were in Building a along with the Bembridge Tamar Class lifeboat receiving maintenance and a Mersey Class representative (12-004) in Paint Shop 2.
From the outside, Building B is almost a mirror image of Building A. But what goes on inside is very different in this paint-free clean area. Here 7-bays handle the assembly stages of newbuilds with two bays presently used for lifeboat maintenance. Again, a mezzanine level runs along the rear of the bays permitting direct access onto the lifeboats housed there with the storage of tools and parts immediately next to where they are needed. When required a raised walkway cell encompasses the hull profile along this side of the production line as well thus enhancing accessibility and safety. To reduce wasted man hours the build and repair bays are clinical in their precision. Dedicated tool bags for dedicated jobs are provided to personnel to avoid time lost sourcing tools or parts with tasks set for each worker daily. Another economy measure is the development of a system where goods are delivered in purpose built jigs to eradicate the need for packaging, associated charges in supply and disposal plus the man hours needed to pack and unpack.
The ALC is supplied by the nearby RNLI Support Centre so that parts are always there when needed. Offices above in the third storey of each building cater for 75 personnel from the design and maintenance departments etc. Efficiency even runs to the parts drawer systems that should enable each part to always be in stock, i.e. nuts & bolts etc. Duplicate drawers for each part are restocked as one becomes empty. The fault finding team is also based on the mezzanine level so are on hand to deal with issues rather than being detached from the scene in an office elsewhere. Overlooking the production line in Building B is an observation room where guests and the representatives of those funding a newbuild can oversee progress. Six Shannon Class all-weather lifeboats will be produced at the ALC per year, the first of which starts production in February 2016 with the next following approximately two months later as the 12-stage rolling production cycle “pulses” every 8 weeks so one lifeboat takes 2 years to complete. The layout of the ALC is “future proofed” to cope with the sizes of future lifeboat generations to be built there along with the long term goal of further enhanced efficiency. Until full production is achieved, hulls & superstructures will still be fabricated at SAR Composites in Lymington and transported to the ALC by road.
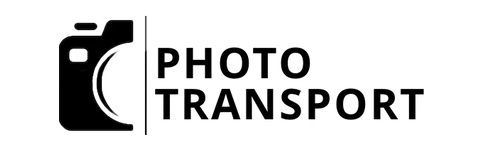
Comments
Sorry, comments are closed for this item